5 factors in transforming the auto supply chain
Vamshi Rachakonda and Roshan Batheri | Automotive News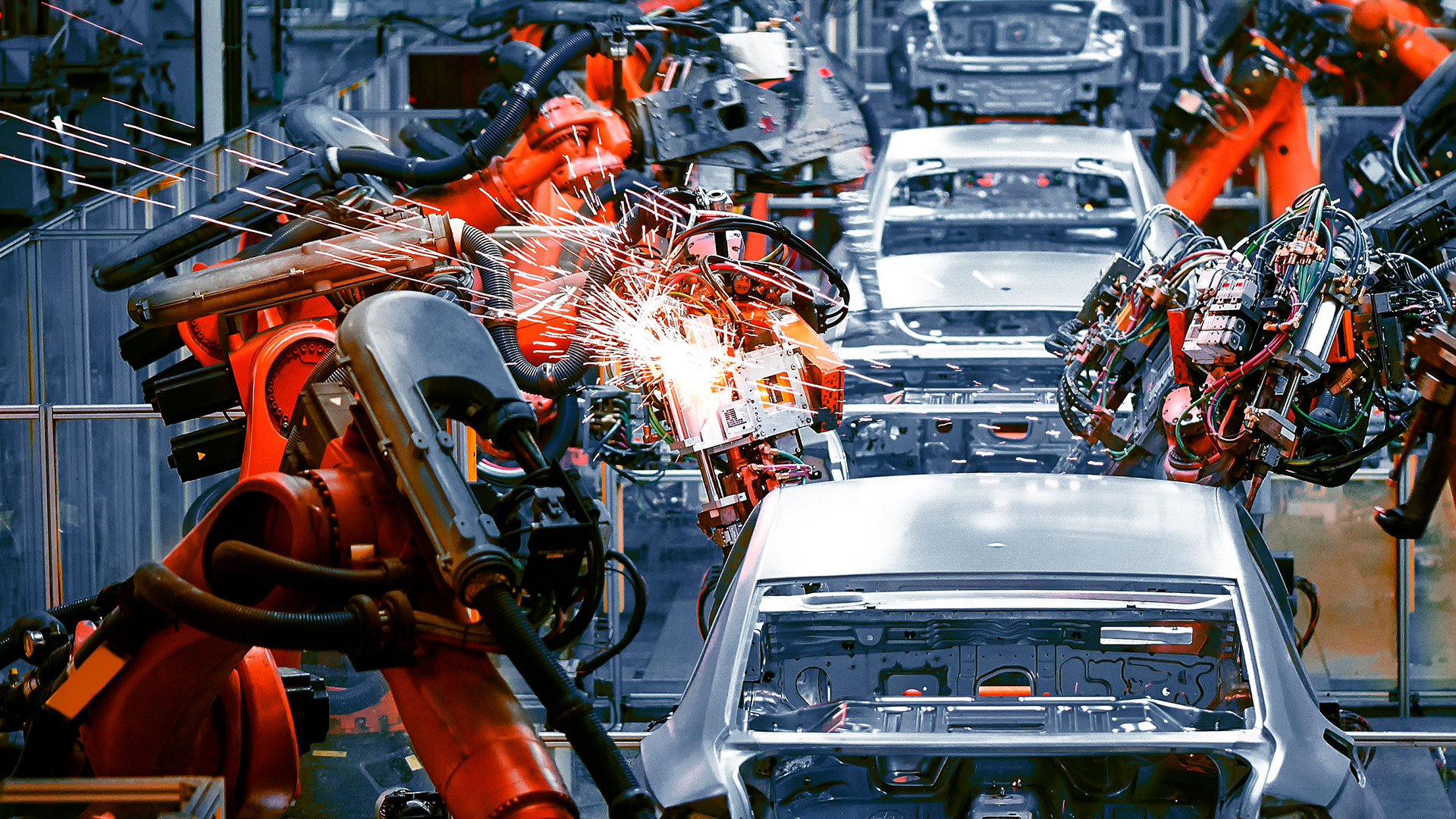
5 factors in transforming the auto supply chain
The automotive industry has undergone significant disruption in recent years. Advancements in electric mobility, autonomous solutions, automotive retail and vehicle connectivity have propelled the sector forward and left enterprises and consumers alike excited for what comes next. Despite all of this growth, the COVID-19 pandemic ushered in challenges, specifically surrounding supply chains. The semiconductor shortage and other geopolitical factors have resulted in supply and demand issues across all functions, which has led many companies in the industry to focus on building a future-proof supply chain that is both flexible and resilient. To ensure preparedness for potential future crises, many auto manufacturers have begun digitizing their supply chains and prioritizing risk management as a part of their strategy. But this cultural and technological shift toward resiliency — with an added focus on sustainability — cannot happen overnight, and there are many elements to consider for automotive companies on this journey. Here are the five major factors impacting the automotive supply chain. 1. Global uncertainties and geographic regulatory guidelines The U.S. auto market is one of the largest global markets, with a combination of import and local production supply chain strategies. Complex global supply chains and triggers such as material shortages, cost pressures, and increased waiting periods and localization guidelines have brought more opportunity for local manufacturing in the automotive supply chain in the U.S., which will in turn make this market more competitive with global manufacturers. While expanding the supply chain here will have a positive impact, the policy formulation and implementation transitions associated with manufacturing typically involve a lengthy time frame. For this reason, it is imperative for automakers to implement the proper infrastructure, which enables data and business insights, in order to establish trust and allow for fast execution and business continuity. 2. Raw material shortages Raw material shortages have resulted in noise around revisiting supply chain strategies. Challenges supplying critical ingredients for vehicle production, such as cobalt, lithium and nickel, have become a major barrier to manufacturing — and many automakers are getting creative to mitigate these shortages. The U.S. is increasing collaboration with Canada to supply battery minerals, while several industry players have begun investing in rare mines and prioritizing a geocentric supply chain model to enhance local mining operations of lithium, cobalt, nickel and graphite. For example, one multinational automotive manufacturing company will extract lithium in California and expects to start production in 2024. Another electric vehicle giant will start mining lithium in Nevada for future battery production. 3. Digital transformation The shift from legacy supply chain technology to more advanced capabilities will allow automotive companies to avoid being negatively affected by what has yet to happen. Many companies are investing in new technologies — Internet of Things, 5G, artificial intelligence, etc. — to build a more flexible and transparent supply chain and avoid unwanted disruption. These technologies have enabled the automotive sector to increase connectivity across all areas of business. Connected consumers, factories, automobiles and supply chains generate a wealth of data and enable manufacturers to identify potential supply issues, increase efficiency and predict timelines more accurately. By improving these operations through digital transformation, automotive manufacturers can enhance their financial liquidity and profitability while streamlining processes and improving customer experience. 4. Changing customer demand The modern consumer has evolved significantly since the early days of car purchasing. The shift to digitization has not only impacted the way that vehicle technology operates, but also how the consumer demands new experiences. Those in the market for a vehicle are looking to automotive manufacturers and dealers for a 360-degree digital buying experience. New retail models allow customers to order a vehicle directly from an auto manufacturer on a one-price model, with no dealership haggling or in-person inventory challenges. This changing customer demand for more digital purchasing experiences impacts outbound logistics as well as supply chain efficiency and cost structure. In addition, the omnichannel retail experience allows for new customization features, which make stress-testing the supply chain even more essential. 5. Sustainability and net-zero ambitions in focus Research shows that 72 percent of automotive companies believe they have made better progress in sustainability than other industries, and many have outlined net-zero goals and environmental, social and governance priorities in an effort to deeply embed sustainability into their strategy. The growth of EVs and sustainable manufacturing has signaled to many leaders that they must address the sustainability of the supply chain and end-to-end product life cycle. In fact, many auto enterprises have made structural changes around vendor selection to include sustainability evaluation parameters and risk assessments, signaling that the green future is high on the priority list. The same methods that can increase supply chain resilience often improve sustainability — and can result in cost reductions. However, creating a sustainable supply chain requires collaboration. An evolving way forward is a transparent and structured collaborative approach among the key stakeholders in the automotive supply chain ecosystem. For example, automakers must rely on Tier 1 and 2 suppliers to help them ensure environmental, social and governance compliance at lower tiers. Collaboration can also reduce waste by ensuring that suppliers produce exactly what is needed. The adoption of environmentally conscious operations in logistics, distribution, warehousing and inventory management can help leaders begin to prioritize a more sustainable supply chain. Technological disruptions are prompting organizations across industries to revisit their supply chain strategies. In the automotive sector, there is a paradigm shift toward a more resilient, data-enabled culture, with a focus on scenario-based planning and dynamic decision layers. While there are many external factors that continue to impact the movement to a more sustainable and flexible supply chain, it is important for leaders to reexamine their road maps and assess where improvements can be made. By viewing these external factors as opportunities rather than impediments, leaders in this space can build a more streamlined, greener automotive future for all.

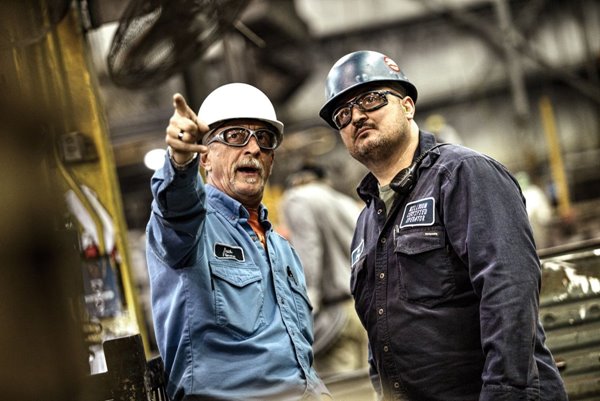