All Hands on Deck For Critical Cupola Replacement
Janelle Bailey | Waupaca FoundryProactive planning and foresight, all-in collaboration, and effective communication resulted in success for a staggering undertaking: replacing one of two cupolas at Waupaca Foundry Plant 5 in Tell City, Indiana, and within a four-week window. The entire project was executed, though truly a “Herculean effort,” according to Bruce Tesch, Director of Melt and Manufacturing Processes, essentially due to the steady and dedicated efforts of all involved.
While the work of the cupola replacement itself was paused for budgetary reasons in 2020, the project began in 2019 and was completed over several phases. Communication and collaboration were paramount among plant engineering, maintenance, operations, and sales personnel, and as many as 15 outside contractors. Plant 5 Project Engineer Dave Bean and a team of engineering peers, Kuttner North America engineers, Jacobs Engineering structural engineers, and Azco industrial contractors, along with the melt and maintenance departments and others worked collaboratively to ensure the successful completion of the entire project. “This was very much like the assembly of a medical team collaborating on a critical heart transplant, the cupola even being the heart of the foundry,” says Dave Bean.
Having been installed and in use since the opening of Plant 5 in 1996, the cupola was aged and beyond further necessary maintenance; this cupola is responsible for ductile iron production. The capital investment included several additional smaller projects, such as changing the separator and replacing the burners with a modern, more efficient style, as well as installing a new oxygen system, changing the design for heavy particle processing. The project concluded with the legacy cupola being dismantled and removed and the new cupola installed—and all through the roof.
The cupola replacement meant a temporarily reduction in plant production by half, presenting some supply risk to customer and manufacturers’ gray and ductile iron casting demand. A tremendous amount of work was completed ahead of time and by everyone involved to minimize risk. The goal was aggressive: replace the cupola in just four weeks. It was successful in large part because of the preparation done leading up to the December 2021 shutdown. Both the sales and customer service teams worked in advance with buyers to determine iron casting supply needs, and build inventory to keep manufacturers running. Other plants also assisted in bank builds resulting in on-time deliveries and no line down situations.
Plant 5 Engineering Manager Shane Hubert and Plant Manager Cody Rhodes-Dawson collaborated to lead the engineering and design teams’ work throughout the project. The cupola replacement undertaking included a number of additional improvements and upgrades to plant processes benefiting both sustainability and utilization targets.
Project engineers, designers, and plant personnel collaborated constantly and led a strict schedule for the cupola replacement to be executed in phases. While budgetary constraints prohibited some upgrades from the initial visionary plan, much of the necessary prep work was done during typical shutdowns. The major installation of the cupola occurred as pieces were moved through the roof. This necessitated accuracy of envisioning the turns and angles by which the largest pieces and parts could be rotated, moved in, and installed afterwards. This was such an act of precision and one piece of the cupola rubbed both sides of the roof upon entry, but with no resulting damage.
Utilizing CAD drawings of the cupola’s new location as well as a contractor’s Point Cloud diagrams – a laser overlay on Plant 5’s CAD drawings and providing the most minute measurements – made certain that every detail was addressed, given the critical egress when moving the cupola parts in. During that discovery phase, it was also learned that a new foundation for the cupola was necessary. The new foundation was poured and cured ahead of the cupola installation, resulting in no additional shutdown time or project creep.
Between December 23, 2021, and January 23, 2022, the old cupola was removed and the new cupola delivered, and all through the roof. The new cupola was then constructed and installed, ready for iron pour tap in four weeks rather than five. (And actually, the cupola was up and running even two days ahead of the four-week mark.) Herculean success on this critical “transplant” and its many additional parts, with kudos to all individuals involved and each doing top-notch teamwork, uniting and collaborating toward this extremely well-executed capital project at Waupaca Foundry Plant 5. Thanks to them, Plant 5’s cupola beats…fires…on!
#iron-casting
#tellcity
#upgrade

Waupaca Foundry Tell City employees working on a Cupola replacement
While the work of the cupola replacement itself was paused for budgetary reasons in 2020, the project began in 2019 and was completed over several phases. Communication and collaboration were paramount among plant engineering, maintenance, operations, and sales personnel, and as many as 15 outside contractors. Plant 5 Project Engineer Dave Bean and a team of engineering peers, Kuttner North America engineers, Jacobs Engineering structural engineers, and Azco industrial contractors, along with the melt and maintenance departments and others worked collaboratively to ensure the successful completion of the entire project. “This was very much like the assembly of a medical team collaborating on a critical heart transplant, the cupola even being the heart of the foundry,” says Dave Bean.
Having been installed and in use since the opening of Plant 5 in 1996, the cupola was aged and beyond further necessary maintenance; this cupola is responsible for ductile iron production. The capital investment included several additional smaller projects, such as changing the separator and replacing the burners with a modern, more efficient style, as well as installing a new oxygen system, changing the design for heavy particle processing. The project concluded with the legacy cupola being dismantled and removed and the new cupola installed—and all through the roof.
The cupola replacement meant a temporarily reduction in plant production by half, presenting some supply risk to customer and manufacturers’ gray and ductile iron casting demand. A tremendous amount of work was completed ahead of time and by everyone involved to minimize risk. The goal was aggressive: replace the cupola in just four weeks. It was successful in large part because of the preparation done leading up to the December 2021 shutdown. Both the sales and customer service teams worked in advance with buyers to determine iron casting supply needs, and build inventory to keep manufacturers running. Other plants also assisted in bank builds resulting in on-time deliveries and no line down situations.
Plant 5 Engineering Manager Shane Hubert and Plant Manager Cody Rhodes-Dawson collaborated to lead the engineering and design teams’ work throughout the project. The cupola replacement undertaking included a number of additional improvements and upgrades to plant processes benefiting both sustainability and utilization targets.
Project engineers, designers, and plant personnel collaborated constantly and led a strict schedule for the cupola replacement to be executed in phases. While budgetary constraints prohibited some upgrades from the initial visionary plan, much of the necessary prep work was done during typical shutdowns. The major installation of the cupola occurred as pieces were moved through the roof. This necessitated accuracy of envisioning the turns and angles by which the largest pieces and parts could be rotated, moved in, and installed afterwards. This was such an act of precision and one piece of the cupola rubbed both sides of the roof upon entry, but with no resulting damage.
Utilizing CAD drawings of the cupola’s new location as well as a contractor’s Point Cloud diagrams – a laser overlay on Plant 5’s CAD drawings and providing the most minute measurements – made certain that every detail was addressed, given the critical egress when moving the cupola parts in. During that discovery phase, it was also learned that a new foundation for the cupola was necessary. The new foundation was poured and cured ahead of the cupola installation, resulting in no additional shutdown time or project creep.
Between December 23, 2021, and January 23, 2022, the old cupola was removed and the new cupola delivered, and all through the roof. The new cupola was then constructed and installed, ready for iron pour tap in four weeks rather than five. (And actually, the cupola was up and running even two days ahead of the four-week mark.) Herculean success on this critical “transplant” and its many additional parts, with kudos to all individuals involved and each doing top-notch teamwork, uniting and collaborating toward this extremely well-executed capital project at Waupaca Foundry Plant 5. Thanks to them, Plant 5’s cupola beats…fires…on!

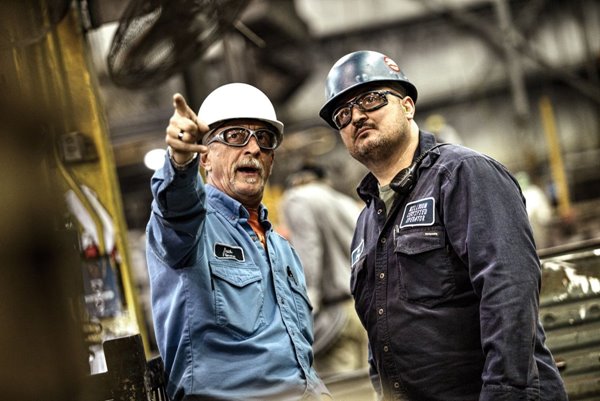
Have a lightweighting, casting conversion, reshoring or other initiative to discuss?
Contact Us
We use cookies and other tracking technologies to personalize content and analyze our site traffic. More information about this is in our Privacy Policy. You can control third party cookies by adjusting your browser settings.