Building Smarter Supply Chains
Robert Boyle | Industrial Equipment News
According to the Logistics Bureau, 69 percent of organizations don’t have full visibility of their supply chains. Why does this matter? Because full visibility is needed to improve manufacturing supply chain operations and reduce costs. For most manufacturers, supply chain data is siloed in various locations—often in multiple spreadsheets—which makes it difficult to uncover opportunities for improvement.
The Logistics Bureau also notes that businesses with optimal supply chains have 15 percent lower supply chain costs, less than 50 percent of inventory holdings, and cash-to-cash cycles at least three times faster than those not focused on supply chain optimization. This is where network optimization comes in. Network optimization provides visibility into all areas of a manufacturing organization’s data, empowering decision-makers with insights they can use to drive actions to improve operations and reduce costs.
Creating a Digital Twin
Trying to manually model an entire supply chain using data from spreadsheets is a labor-intensive, time-consuming, arduous process that can be rife with errors. Network optimization streamlines the collection of a manufacturer’s supply chain data by creating a “digital twin.” The digital twin replicates relevant supply chain data to give a manufacturer the ability to gain a granular view of all its critical data elements. Typical supply chain data elements include:
- Locations
- Volumes
- Origins
- Materials
- SKUs
- Product weight
- Transportation costs
- Throughput costs
Once all of the supply chain data is aggregated into the digital twin, manufacturers can use this granularity to identify their true total costs. It’s important to keep the digital twin up to date— otherwise it becomes an outdated picture of what once was. With an updated digital twin, supply chain managers can see lanes and flows in real-time, enabling them to fully understand what’s going on in their business.
Getting to Actionable Data
Having a manufacturer’s supply chain data in a digital twin is the right first step. But they need to take action based on that data to uncover its true value. The next step in a network optimization study is modeling. Once the data is consolidated in the digital twin, the modeling outputs are then input into sophisticated business intelligence tools to create an easily consumable, visual digital representation of improvements that can be targeted.
With these digital models, manufacturers can determine and compare trade-offs of potential changes to their supply chain network. The can quickly separate opportunities for measurable improvement from initiatives that won’t provide gains — or worse, might cause losses. Visualization tools make it easy to select scenarios, view possible strategies and calculate outcomes.
It’s not a one-size-fits-all when it comes to reviewing digital twin models. It really depends on the industry and the make-up of the manufacturer’s organization. For example, an e-commerce organization with high demand volatility should review and adjust every three to six months. In contrast, a large manufacturer with less demand volatility might opt to review scenarios and make improvements annually.
A Global Network Optimization Study
In 2020, while the COVID-19 pandemic was in full swing, a leading global manufacturer underwent a network optimization study to learn if there were opportunities to improve their supply chain operations and reduce costs. The manufacturer was spending more than $1 billion annually on shipping, delivering 12,000 different types of materials to 19,000 customers across six continents and operating more than 200 facilities across the globe.
After a digital twin was created that integrated the manufacturer’s most relevant data, advanced modeling software was applied to analyze scenarios, identify areas for improvement and provide recommendations that were actionable. Through the network optimization study, the manufacturer learned that much of their annual shipment spend was being wasted.
In the country where the manufacturer was headquartered, they had production plants on both coasts shipping the same products to different regions. The data and modeling also revealed they lacked strict processes for sourcing customers in different regions, managing lead times and booking shipping costs.
The interactive presentation of the data was the eye-opening moment that the manufacturer needed. Their global inefficiencies were in plain view through actionable data and scenarios that provided clear opportunities to correct inefficiencies and optimize their global supply chain network. In the end, the manufacturer discovered the opportunity to save $60 million due to the network optimization study.
A network optimization study can help manufacturers drive performance and improve bottom-line results. The main measure for considering network optimization is whether a manufacturer is ready and willing to make changes to improve their operations and reduce costs. The visibility gained from a network optimization study simply isn’t enough. A manufacturer needs to be prepared to use the insights revealed by the study and take meaningful action to improve their supply chain network.

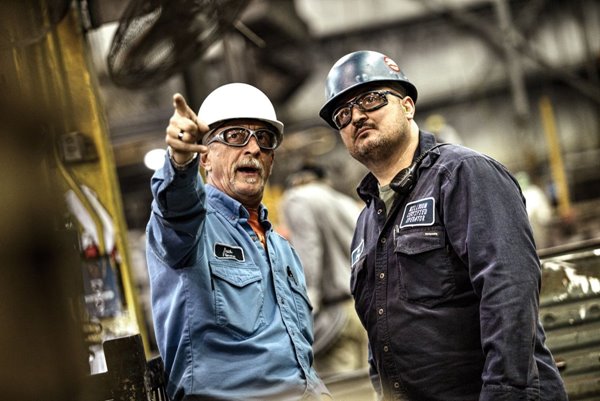