Casting Call: John Gleason
Ally Melby | Waupaca FoundryConstruction worker turned machinist finds purpose in career at Waupaca Foundry
John Gleason started working at Waupaca Foundry’s machining facility in Effingham, Illinois in November 2011 as a machine operator. He then moved into the tooling department in 2016, where he worked second shift as a tooling technician until working his way to first shift. In February 2019, he was promoted to second shift production supervisor.We chatted with John to ask about his new position and time at Waupaca Foundry.
You recently were promoted to second shift supervisor. Tell me about that.
“The second shift supervisor position opened up. Nobody else on the floor was putting in applications for it … so they (supervisors and production) actually confronted me. They came up to me and said ‘Hey we think you would do a really good job at this.’ I put my app in, and the rest, so far, is kind of history. I am excelling at what I do now, and I really love it. It’s pretty stressful, but it’s like any supervisor job. For me, I have somewhere around 45 people underneath me, plus 15 or 20 indirects.”
What characteristics make up a successful supervisor?
“For me, patience, understanding people’s situations. You have to definitely be a leader. You have to be compassionate at times because a lot of stuff happens and you have to react to that accordingly.”
What motivates you to go to work?
“I have to get up and do my part, not to mention that it does pay the bills and everything else, but it gives me purpose. You have to have something in your life that drives you and makes you want to be better and more productive. I’ve found a job in Waupaca, so far, that does that for me.”
What is the most rewarding part of your job?
“The atmosphere here is really good. The sense that I know that when I come in here that the people are doing the best that they can, they work the hardest that they can. We’re putting out a product that we really back and stand behind because, let’s face it, what we make here is a safety part. We have to put everything we have into making these parts that go into these vehicles and keep people safe.”
When you reflect on your time at Waupaca Foundry, is there anything that surprises you?
“I have never been in the automotive field before. It surprises me how many parts a facility like this can actually push out, and it’s amazing how we can do it day in and day out.”
Do you have any untold stories?
“When I was in the tool room, we were known as the dress-up squad. All three shifts would really take it on ourselves to dress-up for Easter and other holidays.”
“Our boss at the time, which was Wade Gray – tool room supervisor – he encouraged it. He would dress up also, so it was fun. The tool room, to me, before I became supervisor was the coolest cast ever. We were always up to no-good antics. We got our job done, of course, but we kept it fun. That’s the key. In turn, that brings up morale because people are seeing that on the floor.”
Is there anything in your Waupaca Foundry career you would have done differently?
“As far as I progressed here at the facility, I think I did it the right way. I started in an entry-level and got to know that, went to the tool room, which the tool room helped me immensely in the position I am in now because now I know both sides of the story when it comes to tooling and how that is implemented on the plant floor so I can help out my team leads.”
Waupaca Foundry is the proud employer of more than 4,500 employees, and 37 percent have been with us for 10 years or more. We appreciate the hard work and dedication of every one of our team members who keep producing the highest quality cast iron components.
Cast your own future jobs.waupacafoundry.com.

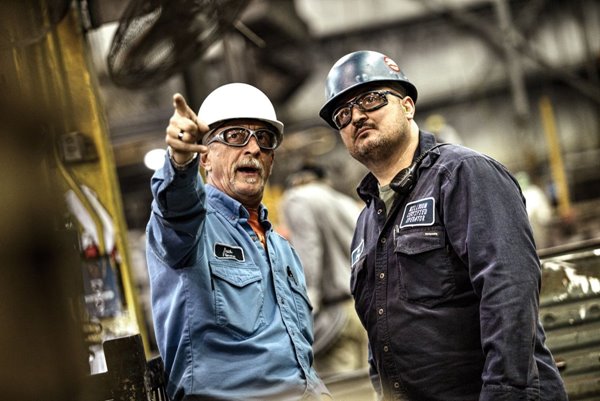
We use cookies and other tracking technologies to personalize content and analyze our site traffic. More information about this is in our Privacy Policy. You can control third party cookies by adjusting your browser settings.