Eliminating the Seven Deadly Wastes
Brian Neuwirth | Assembly Magazine
Eliminating the Seven Deadly Wastes
Manufacturers should evaluate processes to reduce hidden causes of waste
The original seven wastes, or muda, are transportation, inventory, motion, waiting, overproduction, overprocessing and defects. These are often referred to by the acronym “TIMWOOD.” An eighth waste of underutilizing the talent or skills of workers was introduced in the 1990s when the Toyota Production System was adopted in the Western world. As a result, the eight wastes are commonly referred to as “TIMWOODS.”
When manufacturers are able to identify the seven wastes, they can correct and prevent further loss of time, money and other resources.
Transportation
Any multistep production process has its logistical challenges, from transporting and receiving components from suppliers to transferring in-production items from one operational area to another. The longer and more circuitous the transit routes, the more likely they are to generate unnecessary and costly waste.
There is an expense of time, labor and equipment needed to physically move parts and products. In addition, each step in the transportation cycle follows its own discrete set of handling processes, which can increase the risk of delay, damage or theft. Manufacturers with long, complex material handling operations that connect multiple storage locations, remote suppliers, and distant factories must build in expensive, time-consuming safeguards to mitigate the many challenges they face.
Even within a facility, moving people, tools, inventory, equipment and products from one functional area to another can be wasteful and hazardous. Poor workflow design and disorderly factory layout create needless gaps between operations. Bridging those gaps often means workers must lift and carry product or use mechanical transport, both of which can increase the danger of product damage or personal injury. When processes are not located as close to each other as possible or are not arranged in a logical operational sequence, people and products are forced to travel to complete their work. This increases traffic on the factory floor, especially when workers must cover the same ground over and over. In the long run, this excess movement drives down productivity and profitability.
Obviously, not all transportation is unnecessary, but reworking internal and external processes in ways that shorten transportation times and distances is a step in the right direction. Reducing transportation waste goes a long way toward cutting losses.
Inventory
While keeping excess inventory on hand is not a good business practice, many manufacturers still fall prey to hypotheticals. What if something goes wrong in the production process? What if the supplier can’t get a vital shipment out? What if the customer needs more than was forecasted or wants delivery on an accelerated schedule?
Just-in-time (JIT) supply practices are the standard. However, it feels so much safer to have a buffer zone, to stock up in case of emergencies, and be prepared. That’s why excess inventory is so insidious. It’s one of the hardest wastes to root out because it gives us the illusion of control. Unfortunately, it’s an expensive way to hedge your bets.
Aside from tying up operating capital in physical goods, there are also significant noncapital costs associated with holding and servicing excess inventory. Tracking, managing, handling, storing, transporting and insuring physical inventory carry costs that can add up quickly and are generally not recoverable. There is also a risk of inventory loss, damage, deterioration, theft or obsolescence.
Inventory buildup can be driven by overproduction, poor planning, process imbalances, inefficient workflow, over-ordering to qualify for bulk discounts, or any of a range of other hidden factors. It can be stressful to drop inventory to JIT levels, but right-sizing inventory can expose underlying problems that may need to be addressed. Taking stock of inventory practices allows manufacturers to shore up the supply chain, shorten lead times and streamline production processes.
Excess Motion
From figure skaters to basketball players, gymnasts to quarterbacks, top athletes train hard to channel all their energy into useful movement, not waste it on inefficient motion. As sports technique expert and biomechanics specialist Michael Yessis, Ph.D., explains it, “the less energy expended during execution of a sport skill, the more efficient is the movement.”
Production lines and distribution processes may never be as beautiful as the movements of a gifted athlete, but manufacturers can implement similar techniques to decrease unnecessary motion, since it is detrimental to performance. Capacity can’t be increased at the expense of efficiency.
Any time workers are forced to spend time searching, retrieving, bending and lifting to fulfill their job functions, they are not operating at peak performance nor adhering to good ergonomic practices. If tools are disorganized or must be located, repaired or assembled before use, the operation is not using resources efficiently. When equipment must be transported to and from distant storage areas, this is built-in unnecessary movement.
Excess motion increases the risk of worker injury as well as increases wear and tear on tools and equipment. This can lead to potential product loss or damage and increased congestion in work areas, without adding any value to the product or process.
In virtually every sport, the factors that influence athletic mobility are observed, measured, tracked, modeled, studied, tested, analyzed, compared and modified. The findings are used to develop techniques that build speed and endurance, eliminate friction, reduce effort, improve coordination and decrease the risk of injury. Operational goals should be treated the same way. Although the resources involved in sports and industry are different, the same principals of movement efficiency apply.
Manufacturers should look at every step in production. Are heavy items stored on hard-to-reach shelves or out-of-of-the-way locations? Are necessary tools and components missing in action at the time and place they’re needed? Do workers need to take the long way around just to get the job done?
Unlike passive wastes that may be difficult to identify and measure, wasteful motion actively depletes energy and efficiency, making it easier to spot and correct. By eliminating steps, shortening distances and streamlining operations, manufacturers can move closer to peak performance.
Waiting
In manufacturing and distribution environments, rhythm is essential. A smooth, steady, predictable flow ensures that each critical component—tools, parts, materials, labor, equipment and information—is available in exactly the right form and quantity at the exact moment it’s needed. Anything that disrupts or interrupts the rhythm at any point in the flow creates downstream delays. Unanticipated delays are so common, in fact, that time spent waiting is now the second most costly form of waste in many operations.
A few of the most common causes of delays are waiting for a previous step in the production cycle to be completed; waiting for materials to be transported from another location; waiting for information, authorization or confirmation; waiting for a missing item to complete a batch; or waiting for quality or service issues to be resolved.
Waiting time doesn’t always mean that work completely stops; breakdowns, slowdowns and stalls can sometimes hide within the production process. Most operators want to play by the rules, so rather than going idle or powering down equipment, they practice “working while waiting.” Working at a slower pace while waiting for a needed component maintains appearances but continues to waste labor efficiency and often saps momentum and motivation, as well.
Waiting can be a symptom of unbalanced processes, mismatched cycle times, inconsistent replenishment schedules, poor communications pathways, improper inventory management, unreliable equipment, insufficient maintenance strategies, or any combination of these factors. Whatever the cause, the effect is that the operation doesn’t run smoothly and productivity falls short of its potential.
Overproduction
In an industry where so much emphasis is placed on boosting productivity, it might seem counterintuitive to name overproduction as the primary source of waste. Yet across most organizations, it consistently is. That’s because the volume of work produced does not necessarily correlate with the value of that work.
If a product is manufactured sooner than required or in greater quantities than is needed, time, labor, and materials are wasted. What’s more, having too much product on hand creates excess inventory, which increases the costs of inventory storage and management. If the product is seasonal, it’s now more likely to end up as scrap. If the product is perishable, it’s now probably headed for a landfill. Any time more product is made than sold, you are producing volume without creating value.
In any discussion of organizational waste, overproduction means more than outputting ill-timed or excess manufactured goods. Other common examples of wasteful overproduction include overpackaging; scheduling meetings more often than needed; generating and distributing too much paperwork; creating reports with more detail than recipients want or can absorb; keeping labor and equipment on standby; and duplicating systems or running redundant processes.
The solution is to balance volume and value by carefully calibrating plans and processes so that production syncs with inventory needs. It’s not a matter of how much output, it’s whether that output is available, accessible and acceptable when and where it’s needed. That’s where the value will be measured. Too much of even a good thing is too much, and there’s nothing productive about that.
Overprocessing
Is there such a thing as too much value? After years of lessons on “continuous improvement” and “the pursuit of excellence,” it’s tempting to believe that raising standards is always a good thing. However, that’s often not the case, especially in manufacturing and distribution operations. In those instances, adding what is incorrectly perceived as value actually creates waste—wasted time, labor, parts, materials, and even equipment capacity and lifespan.
The classic example of overprocessing is painting a mechanical part that is never seen post-assembly. Unless that coat of paint is necessary to prevent corrosion or improve function, it’s unlikely to be worth anything to the customer. Would the customer be willing to pay extra to have an unseen part painted? Of course not. Yet the manufacturer is paying for it with extra materials, added labor, longer cycle times, and probably additional health and safety requirements. If a painted finish adds no customer value, why do it at all?
Of course, manufacturers want to give customers their money’s worth. That means providing a quality product that meets their needs. It doesn’t mean providing a product that is better than it needs to be. A product should meet the customer’s performance standards consistently, but no more.
Overprocessing generally begins with good intentions or an abundance of caution, and often gets its start at the design stage. Engineering may call for unnecessarily tight tolerances. Designers might specify expensive or hard-to-procure materials when a cheaper, more plentiful material would do just as well. Sales might push for machined and polished components based on presentation more than on end-use requirements. In addition to the cost of meeting excessive standards, there is also the burden of measuring, testing, verifying and maintaining the overzealousness.
Manufacturers may implement standardized work practices to ensure efficiency and uniformity. In an attempt to go the extra mile, diligent workers might go above and beyond production standards, introducing variations that consume extra time and resources.
To minimize waste, companies should examine whether processes can be combined, compressed or eliminated. Alternative methods and materials can also allow for waste reduction. Having a clear understanding of what the customer values provides insight to improve production methods, eliminate unnecessary work and streamline your processes to eliminate waste. Every non-value-adding step in the process is a gift to the customer, an unpaid-for, unacknowledged and unappreciated extra that costs dearly.
Defects
Defective products can take a chunk out of profitability but can also damage a company’s reputation. When customers must reject shipments, face delays to allow for rework, or encounter their own production problems because of quality issues, they lose confidence in the supplier’s performance. When production errors do happen, it’s critical to quickly identify the cause and take immediate corrective action. Correcting defects is not an inexpensive undertaking as there are costs associated with discovery, problem-solving, rescheduling replacement materials, equipment resets, rework, paperwork, and expedited transport and delivery.
A product is considered defective when it deviates from prescribed quality standards or specifications. The causes can range from use of substandard materials and components to incorrect assembly to faulty equipment to operator error. Regardless of cause, scrapping defects is a waste of time, effort, energy, equipment and materials, not to mention replacement costs.
Much of that waste can be avoided by taking preventive action before defects occur. For example, products can be designed to prevent incorrect assembly. Procedures and controls can be standardized so that different operators on different shifts produce consistent quality. Materials and components should be inspected prior to being introduced into production. Transportation and handling should be minimized to avoid damage. Equipment and environments should be maintained to stabilize production conditions. Operators should be trained to spot defects and stop the line for corrections. Quality should be rewarded to encourage employees to minimize waste.
Lean manufacturing means creating more value for customers with fewer resources. At UNEX, we are firm believers in lean manufacturing and use many of its principles in our own manufacturing process. We design all our products and services to maximize customer value while minimizing waste.

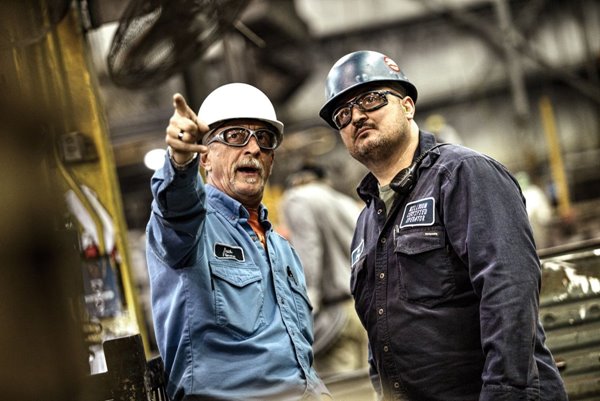