Five Ways to Achieve Lightweighting Objectives with Iron Castings
Steven Kitzinger | Waupaca FoundryThe Corporate Average Fuel Economy (CAFE) standard is set to hit 54.5 mpg in 2025, so it's no surprise the auto industry is aggressively pursuing ways to increase fuel efficiency. The Center for Automotive Lightweighting's Web site states that the use of lightweight materials in vehicles will significantly increase fuel efficiency and cut emissions. As the market takes a serious step towards increasing fuel economy, the topic of material substitution is at the forefront. Gray and ductile iron material is not exactly perceived as lightweight. But, use of this higher-strength iron, allows for design engineers to use less material. Now we're talking.
To achieve lightweighting objects—regardless of material selection—early design collaboration with your supplier is crucial. Early design collaboration with your iron casting foundry that combines tooling engineering, metallurgical expertise and computer simulation will result in iron castings that may reduce weight, lowers total landed costs, increases quality, assure part consistency and meet or exceed performance requirements; all the items OEMs and Tier 1s seek from its suppliers. Many decisions made during the design, specification and sourcing stages of an iron casting can lead to components that are lighter and stronger.
Here are five ways your iron casting supplier can help you achieve your lightweighting objectives:
- Implement a heat treat and use Austempered ductile iron (ADI)
- Reposition the gating and riser locations
- Thin iron casting sections or walls
- Remove a core
- Change the location of the parting line
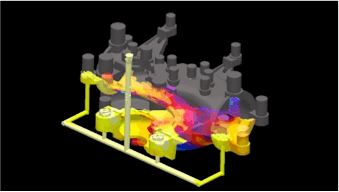
It all starts with MAGMA® Flow Analysis, an electronic simulation showing how molten iron flows and solidifies as it is poured into the casting mold. MAGMA® Flow Analysis allows foundry engineers to pre-determine iron flow and identify turbulence, solidification, temperature, and pouring issues relative to the quality of the final cast part. While MAGMA® Flow Analysis is not a lightweighting tool itself, it is a valuable tool that tells foundry engineers and their customers the options they have to achieve a lighter weight part including the five we outline here:
Austempering or Heat Treating the Ductile Iron
A material selection upgrade to ADI over traditional ductile iron is a tool used for lightweighting. In particular ADI is two to four times stronger than standard ductile iron. Using ADI drives the weight of the casting down making it much lighter thanks to a reduction in structural mass requirements. When using ADI, strength requirements can be maintained while utilizing thinner sections, for an overall reduction in the weight of the component. The practical advantage to ADI is manufacturing cost, since it is much less expensive to produce.
Repositioning the Gating and Riser Locations
If a MAGMA® Flow Analysis shows that an area of a mold will be difficult to fill resulting in porosity issues, it may be possible to reposition the gating or riser to overcome the porosity issues. Lowering the porosity in one or more areas of the casting can lead to there being more mass than needed in those areas. Removing mass and achieving an acceptable level of porosity will lead to a lighter part as long as that particular area is not necessary for strength or a machining location. Only through early collaboration can these questions be identified and answered.
Thinning Sections or Walls
Most if not all part designs call out an acceptable level of porosity throughout the print. Again, using MAGMA® Flow Analysis, engineers can tell whether the iron flow will cause porosity to be above or below the acceptable level. Foundry engineers are not strangers to following porosity specifications. There are cast components where there is quite a bit of mass resulting in a porosity level that is far below what is specified on the print. If we get a commitment from the purchaser to allow a higher level of porosity, but still below spec, we may be able to remove mass to reduce weight. However, this gets tricky because we may end up aggravating or creating more porosity in another area to achieve mass removal in this area. Again, early collaboration in the casting design will make all the difference in the success of this lightweighting effort.
Removing or Eliminating a Core
This would take a commitment from the casting design engineer and the casting supplier early on in the design process. In some castings, the core simply cannot be removed due to internal features.
Change the Location of the Parting Line
Changing the location of a parting line is a fifth tool in the box that can be used for lightweighting. Imagine a cast iron vase that stands vertically on a table. The top of the vase may have a diameter of two inches and as you move down the vase, the neck narrows to one inch. Then as you move further down the vase the belly of the vase opens to four inches. In the vertical green sand molding process, in order to remove this vase from the sand without destroying the part, a core would have to be used around the neck of the vase. Without a core, material would have to be added to the vase so that the vase has the same diameter throughout. This would make the vase heavier. However, by laying the vase on its side, changing the parting line to run along the curves of the vase, there would be no need for a core. There would also be no need to add material to the vase allowing the vase to be lightweight.
Again, early design collaboration between the purchaser and the casting supplier will maximize lightweighting outcomes and in best cases, lowers the total landed cost of the part, increases quality, improves run consistency and heightens its performance. Involve your casting supplier early on in the design; you'll be happy you did.

See how Waupaca Foundry reduced the mass of a ductile iron differential case by 41% and machined stock by 60%.

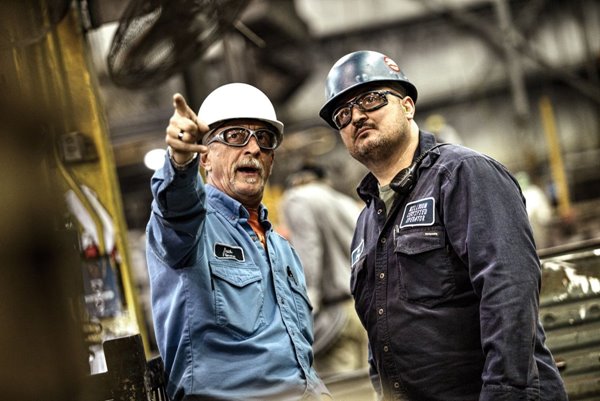