Foundry of the Week: Waupaca Foundry

Foundry of the Week: Waupaca Foundry
At Waupaca Foundry, capacity is more than volume.
It’s our capacity to keep promises so our customers can expect tomorrow’s deliveries on time, as well as tomorrow’s innovations. It’s the capacity to contribute value and solve problems at every stage of design and production. It’s leveraging integrated services to cut costs and turnaround time, while flexing production for our customers’ volume needs. And it’s the capacity that our global network to create supply chain efficiencies, bring value added engineering innovations, and offer material solutions—for confidence and peace of mind.
Waupaca Foundry casts and machines iron casting components for global markets including automotive, commercial vehicle, agriculture, construction, material handling and other industrial sectors. We produce gray iron and ductile iron castings including austempered ductile and HNM high-strength ductile, melting more than 10,000 tons a day. Iron casting components up to 350 pounds (160 kilograms) are produced using one of 35 vertically parted, high pressure molding machines by a workforce that puts generations of foundry and machining expertise to work for our customers every day.
Operating seven foundries and two machining and assembly plants, Waupaca Foundry employs more 4,500 people. Locations are strategically concentrated, yet operationally decentralized, which streamlines the metalcasting supply chain.
Since 1955, Waupaca Foundry has continuously improved in the areas of safety, quality, productivity, and reliability. Our design engineering, high volume melting capabilities, custom-built vertical green sand molding equipment, and automated finishing systems minimize post-process machining requirements and maintain controlled chemistry for consistent machining—all resulting in best-in-class iron casting components.
CASE STUDY >> Download
Rising fuel efficiency and emissions standards are driving an increased demand for lightweight automotive components. While aluminum materials are commonly specified, Waupaca Foundry in collaboration with Hitachi Metals America have the capabilities through design optimization and high-strength ductile iron to meet weight reduction goals while generating significant cost savings and a stronger component.
Situation
To meet its lightweighting objectives initially, an automotive OEM selected a 13.34 pound (6.05 kg) aluminum forging for its front steering knuckle over a 23.81 pound (10.80 kg) ductile iron concept. Although the decision for an aluminum component achieved the weight reduction goal, it resulted in a considerable cost increase when compared to ductile iron.
After the initial launch of the aluminum component, the OEM asked Hitachi Metals to explore a lightweight ductile iron knuckle to replace the aluminum component. To be successful, the ductile iron solution needed (or must) weigh 17.6 pounds (7.98 kg).
The front steering knuckle connects various suspension and brake components to the wheel-end assembly. Key requirements for fit and function included:
- Provide secure mounting to 10 different suspension and brake parts.
- Avoid interference with other adjacent components.
- Strengthen to handle a variety of extreme driving events.
- Ensure reliability for a minimum of 10 years under severe driving conditions.
- Prevent brake noise and deliver desired handling and ride.
- Provide clearance to surrounding parts in all possible driving situations.
Solution
Hitachi Metals design engineers developed a solution to meet the key requirements by redesigning and optimizing the shape of the knuckle using a high-strength ductile iron material.
Testing verified the parts strength, durability and stiffness. Continued optimization of the casting achieved the lightweight target of 17.6 pounds (7.98 kg).
Win-Win
The new design not only fit into the components existing space, but it also met all of the customer’s requirements including stiffness, strength and durability. The weight of the optimized knuckle design was 16.25 pounds (7.37 kg), under the targeted goal of 17.6 pounds (7.98 kg). The weight difference between the optimized ductile iron knuckle and the aluminum forging was reduced to only 2.91 pounds (1.32 kg). In addition, the OEM realized a 40% cost savings and received a 20% stronger component.
- Ductile iron knuckle is 20% stronger and has 25% higher stiffness vs. aluminum solution.
- Achieved 30% weight reduction over the original ductile iron design.
- Narrowed weight difference between the ductile iron vs. aluminum solution to 2.91 pounds (1.32 kg).
- Realized a 40% cost savings per casting.

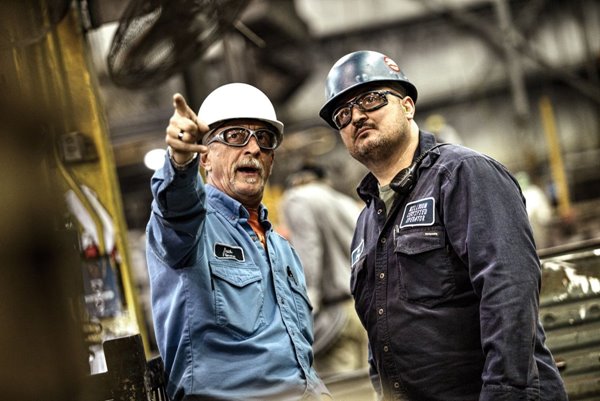