General Electric's GE9X engine undergoes further testing of 3D printed components
Corey Clarke | 3D Printing IndustryGeneral Electric have been advancing additive manufacturing in aviation. They have recently gained clearance for their LEAP engine nozzle which is intended for smaller single-aisle aircrafts. The LEAP has been approved by the Federal Aviation Administration and the European Aviation Safety Association. The GE9X engine for Boeing’s 777x will also include 3D printed fuel nozzles. It is believed that GE’s acquisition of 3D printing companies Concept Laser and Arcam was motivated by large order numbers for these fuel nozzles.
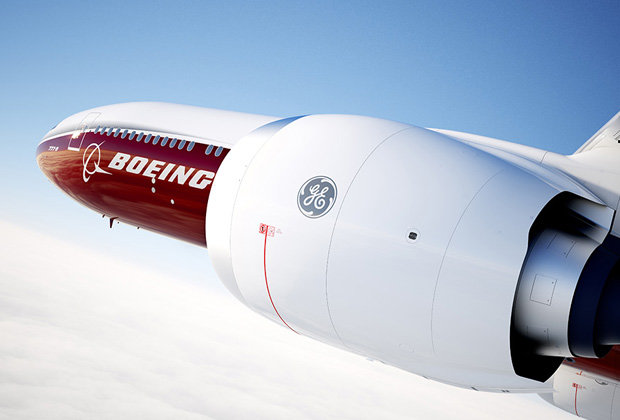
Dust and debris
The engine was meticulously tested in Ohio to handle the effects of dust and debris during 1,800 operational cycles. However, the sheer amount of dust the engine was exposed to meant the testing was equivalent to over 3,000 take-off and landing cycles. The GE9X components coped well with the testing and GE were pleased with the results.
Ted Ingling, GE9X general manager at GE Aviation, explains why testing in these conditions is important,
DUST AND DEBRIS ACCUMULATE ON THE EXTERNAL SURFACE OF THE AIRFOILS AND CAN DEGRADE THE INSULATION COATINGS. THEY CAN ALSO COLLECT ON INTERNAL COOLING CIRCUITS OF THE BLADES AND NOZZLES AND DEGRADE THE COOLING EFFECTIVENESS. BOTH FACTORS CAN LEAD TO DURABILITY ISSUES. THESE DEMONSTRATOR TESTS ALLOW US TO GET AN ACCELERATED UNDERSTANDING OF HOW OUR NEW DESIGNS AND MATERIALS PERFORM IN ALL ENVIRONMENTS, INCLUDING THOSE PRONE TO HIGH AIRBORNE DEBRIS.
3D printed components
Using the GEnx testing engine, GE assessed new additive manufactured blades for the engine’s turbine. Produced by Avio Aero, the “lightweight low-pressure turbine titanium aluminide (TiAl) blades” are the most efficient cooling circuits ever produced according to GE.
Avio Aero are a manufacturing company operating from Italy, and were acquired by GE’s aviation arm in 2013. The blades they have produced will be part of the biggest aeroengine turbine ever made with a diameter of over 80 inches.

Ceramic Matrix Composite
The ceramic matrix composite components of the GE9X are a huge advancement for the aviation industry as they move towards new materials. According to Ingling, the CMCs performed very well and continued to “prove their value“.
CMCS CONSIST OF SILICON CARBIDE CERAMIC FIBERS AND CERAMIC MATRIX AND ARE ENHANCED WITH PROPRIETARY COATINGS.
The CMCs are a third of the weight compared to metal yet with twice the strength. Through this reduction they improve fuel efficiency and durability. The GE9X is 10% more fuel efficient compared to its predecessor according to GE. In addition, these CMC components vastly improve cooling compared to metal.
The GE9X will begin certification testing in the first half of this year with engine certification expected in 2018. The engine already has nearly 700 orders.

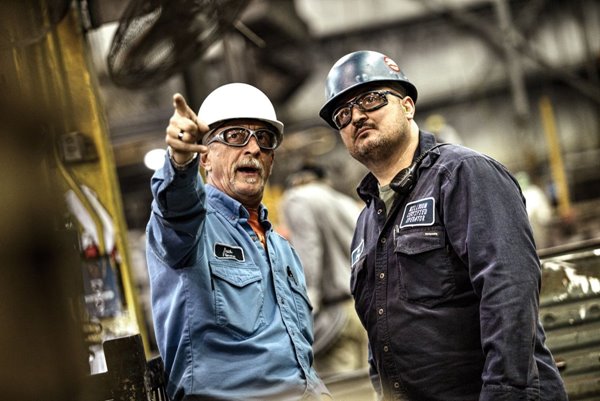