"Waupaca had been a pioneer in the development and use of this technology in it's manufacturing methods. I'm confident that the impact will effect the safety and security of many foundrymen and their families for years to come." - Rolland Smith, regional sales manager for Engis Corporation
Waupaca Foundry Replaces Wheels on Stand Grinders
Hanna Henrich-Waller | Waupaca FoundryDiamond Wheels Replace Bonded Abrasive Wheels in Risk Reduction Project
Improving Workers Safety in the Mill Room
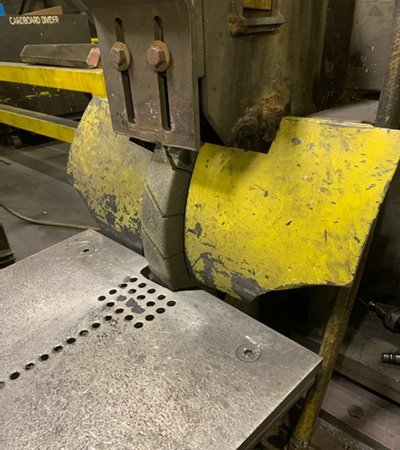
An abrasive bonded wheel is essentially small pieces of stone that are glued together by fiber glass.
Bonded abrasive wheels have a high risk of failing because of the stones disintegrative nature. When the wheels disintegrate the debris that it ejects causes trauma. While an abrasive wheel has not failed at Waupaca Foundry, the process engineering team desired to be proactive and find a safer wheel solution for grinding ductile iron castings.
As opposed to the bonded wheel, a diamond wheel is constructed of a solid piece of stone.
Jon Loken, the Director of Health and Safety at Waupaca Foundry explained, “Although there are many controls in place at Waupaca to mitigate that risk, the risk is always there.” The diamond wheel completely eliminates any risk posed with an abrasive wheel. A diamond plated wheel will never fracture in the way an abrasive wheel would.
An Abrasive wheel also produces excess amounts of dust, requires multiple adjustments and periodic wheel dressings to maintain performance, making production less efficient. While the diamond wheel reduces the dust production, eliminates any adjustments, and requires no wheel dressings.
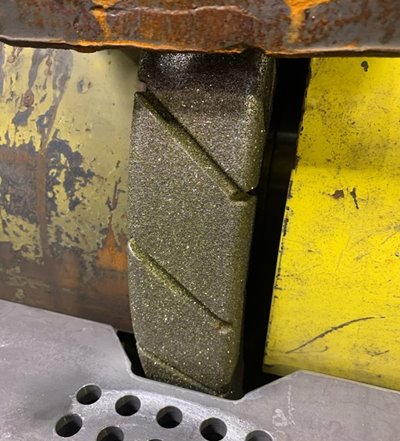
Replacing the abrasive wheel requires a higher RPM to operate the stand grinders with the diamond wheel. It was necessary to refurbish the stand grinder machines to make the switch. The machines were fully refurbished and operational by early 2021, and are preforming exceptionally well. Moving forward, refurbishng is planned to be done on site while it is implemented throughout the rest of the company.

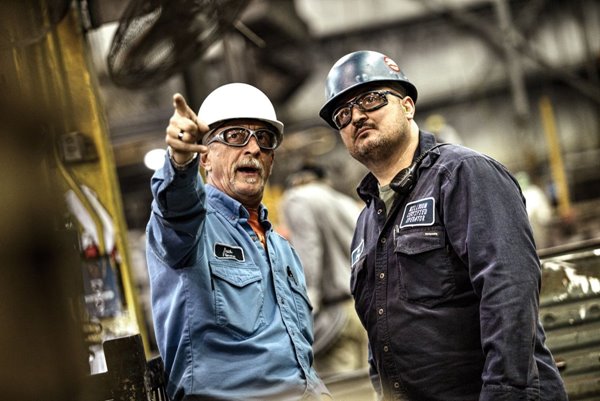
Have a lightweighting, casting conversion, reshoring or other initiative to discuss?
Contact Us
We use cookies and other tracking technologies to personalize content and analyze our site traffic. More information about this is in our Privacy Policy. You can control third party cookies by adjusting your browser settings.