Looking at Castings Environmental Impact Across Their Life Cycles
Jeremy Lipshaw | Casting Source
Looking at Castings Environmental Impact Across Their Life Cycles
The transport sector is responsible for approximately 23% of global energy-related CO2 emissions and is expected to increase at a faster rate than other energy end-use sectors. To mitigate this impact, automobile fuel economy regulations such as EPA’s Corporate Average Fuel Economy (CAFE) standards have been adopted. While effective at improving fuel economy, these automotive regulations are limited to only reducing the CO2 and other greenhouse gas emissions from the tailpipe. Consequently, these regulations ignore the emissions due to producing the components within the automobile and the recycling or other end-of-life impacts that can lead to an unintended increase in greenhouse gas emissions over the life of a vehicle.
Life cycle analysis is a relatively new discipline that incorporates all major phases—production, use and recycling/end-of life—of a product or a process life cycle to calculate total impacts. It is quickly becoming a key tool for academics and industry analysts and has even started to be used within the regulatory environment. The European Commission calls life-cycle thinking “the best framework for assessing the potential environmental impacts of products, processes and systems.” Moreover, the EU already has existing legislation directly based on life-cycle analysis, which requires the calculation of life-cycle greenhouse gas emissions of biofuels. Within the U.S., California has adopted a Low Carbon Fuel Standard. Furthermore, many solutions for industry to adapt to life cycle analysis already exist, such as open-source software
and models.
The spread of life cycle analysis through regulatory programs indicates that similar approaches may become the preferred calculation method for limiting greenhouse gas emissions. Researchers at the Institute of Environmental Technology in Berlin have drafted many different process options to adopt it into governmental policy, including those based on existing ISO standards.
Due to their recyclability and lower embodied energy, castings have the potential to be more sustainable in this framework, but more data is needed to quantify the impact.
Castings and Life Cycle Analyses
An extensive literature review discovered only a limited number of casting-related life cycle analysis that included the use-phase. Rather, most of the literature focused on the energy and costs during production and recycling. This included two Life Cycle Inventory databases for cast aluminum and cast magnesium that provided production and recycling inputs, which can aid future analysis containing all major phases.
While production and end-of-life impacts can inform producer decisions, automotive suppliers evaluating new materials will be looking for the entire life-cycle story, as it is misleading to only report the production and end-of-life phases. In one example, 79% of total life-cycle greenhouse gas emissions of the VW Golf VII vehicle (driving 20,000 km or 12,400 miles yearly) come from the use-phase. Even with the databases available for two major casting materials, only three studies were found that included all three phases––production, use and end-of-life––for cast components:
- “Primary Manufacturing, Engine Production and on-the-road CO2: How can the Automotive Industry Best Contribute to Environmental Sustainability?” 38th International Vienna Motor Symposium (April 2017).
- Jhaveri et al., “Life cycle assessment of thin-wall ductile cast iron for automotive lightweighting applications,” Sustainable Materials and Technologies, Vol. 15, pp. 1–8 (2018).
- Simone Ehrenberger, “Life Cycle Assessment of Magnesium Components in Vehicle Construction,” The International Magnesium Association (May 2013).
This list is almost certainly non-exhaustive, but it displays the lack of research into this topic for castings. Furthermore, the scope of life cycle analysis work in castings is limited: All three studies only compare to other casting processes and do not compare to other material processes.
Arguments for Why Castings May Have a Lower Environmental Impact
Despite the lack of life cycle analysis research into castings, several plausible reasons explain why castings may have a lower life-cycle energy and greenhouse gas impact than other forms of processing.
In the production phase, castings have a lower embodied energy per kilogram than other processes using the same material (Fig. 1). This is most likely because castings are the shortest path from raw materials to a finished product. As a caveat, while embodied energy is not equivalent to greenhouse gas emissions over a product’s full life cycle, it is a significant component of life-cycle emissions. Consequently, assuming the same electrical sources, a decrease in embodied energy will also have an associated decrease in greenhouse gas emissions over the full life cycle of the product.
During the use-phase, the largest influence on fuel consumption and therefore energy and greenhouse gas emissions, is vehicle weight. Since metalcasting is a near net-shape process that can minimize the amount of machining, finishing, and number of parts per component, castings provide excellent opportunity for lightweighting.
For example, as discussed in a recent Casting Source article, “3 Ways Vehicles Are Reducing Weight,” converting a steel stamping to a magnesium casting resulted in 19.4 lbs. of mass savings and part number consolidation (Fig. 2). In another example from the same article, converting an aluminum stamped assembly to an aluminum casting led to a 20% weight savings and part number consolidation (Fig. 3). Part number consolidation may translate to cost-savings, and the mass savings will translate to a reduction of greenhouse gas emissions in the use-phase.
As scrap metal accumulates from different metal processing streams, chemical impurities in the scrap become more concentrated. Due to the high-purity material specifications for wrought metals, fabricators cannot use a significant amount of scrap material for production. This specification is not as strong for cast components. For instance, wrought aluminum can be recycled into cast aluminum components, but the reverse is unlikely. Recent literature suggests that the baseline secondary content values for wrought aluminum are 0%, while they are 85% for cast aluminum. Similarly, baseline secondary content for flat, long and cast steel are 5%, 85% and 100%. Because castings are inherently more recyclable, the energy and greenhouse gas emissions in the end-of-life phase also will be lower.
Castings hold great promise to be more sustainable than other processes for the same base material, even when lightweighting is not feasible. Because of castings’ edge in production and recyclability, their production may still result in a net savings in energy and greenhouse emissions while simultaneously providing a low-cost solution for automotive suppliers. Ultimately, in a life cycle analysis-focused regulatory environment, the casting industry could reasonably argue that their process is the most sustainable. However, to maximize the effectiveness of this argument, thorough castings life cycle analysis research is needed.

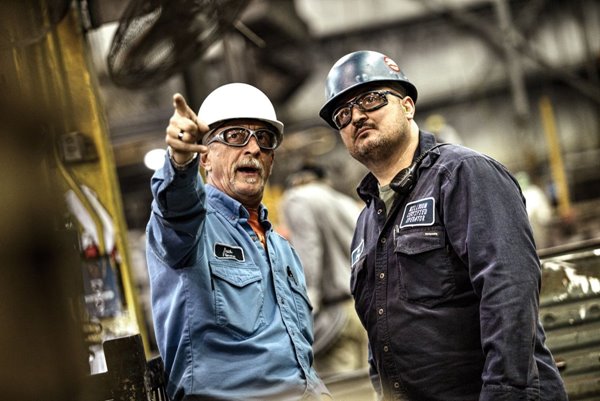