National Technology Day
Ally Melby | Waupaca FoundryWaupaca Foundry has been a forward user of technology since its inception in 1955 and has continually undergone significant technological transformations. Most notably: In 1967, we installed an automatic vertical molding line – which was the first of its kind in the United States – to improve efficiency. In the early 1990s, automation was implemented into our mill rooms and so began the gradual transition away from the manual grinding of castings. In 2019, we began a mill room expansion project at Plant 2/3, including the installation of two new robotic finishing cells (with more updates to come).
While technology has become the forefront of how we conduct our operations, a few of the largest impacts have been on our casting quality, efficiency in energy usage and the changing nature of labor we house.
Casting Quality
According to the American Foundry Society, 90 percent of all durable goods depend on metal casting components, emphasizing the need for top-notch castings to be produced.
At Waupaca Foundry in the 1960s, iron castings were hand-poured with the use of a bull ladle. Today, we utilize an automated process that allows for unmatched reliability and casting capability; Our molding line is 30 percent more productive than our competitors.
Hand-drawn sketches and blueprints were once used to draw casting designs. Today, casting designs are all computer-generated, and we use MAGMA 3-D Solidification Modeling to project casting fluid flow, simulate solidification, iron flow and cooling long before castings are sampled or mass-produced. Additionally, we use Laser-Scanned Dimensional Analysis to scan parts before they are poured to assure the castings are effective and consistent. If not, changes can be made before production. Today, the industry widely uses this technology. Waupaca Foundry is proud to be among the first.
Recently, Waupaca Foundry evolved with the introduction of additive manufacturing as a means to launch parts faster while bypassing design constraints (The first instance of additive manufacturing at Waupaca Foundry being 3-D printing cores and 3 D printed molds).
Energy Efficiency
Since 2004, Waupaca Foundry has executed many energy conservation programs with the help of technology.
In 2008, Waupaca Foundry implemented a closed-loop heat recovery system that utilized the heat generated to melt iron to be recycled back into the plant – accounting for 70 percent of the plant’s heating requirements in the winter. Not only was the project environmentally friendly resulting in the reduction of 4,600 metric tons of carbon dioxide per year, but it was also cost-efficient – saving approximately $900,000 annually.
After, Waupaca Foundry set forward on a 10-year sustainability journey company-wide, which included becoming a more energy-efficient company by reducing energy usage by 25 percent.
From the program baseline year of 2009 to 2018, we had reached a cumulative energy intensity improvement of 21.3 percent.
In 2011, our Marinette, Wisconsin location installed a closed-loop cooling water system, which reduces water cooling demands, resulting in a near savings of 225,000 gallows of daily water usage and zero non-contact cooling water discharges. The system has also been implemented at our locations in Waupaca, Wisconsin; Tell City, Indiana; and Etowah, Tennessee.
In general, we monitor machines’ capabilities through metering to reduce energy waste and improve energy efficiency. Robots standardize casting processes, which reduces the likelihood of human error on a casting, which in turn reduces the energy needed to re-manufacture an insufficient part and instead optimizes it.
Nature of Labor
With greater sources of advanced technology present in our facilities, the nature of labor for our team members has changed.
With our robotic cells, team members can take on higher-skilled positions, which results in higher wages. The work, overall, is safer, and the robots taking on the heavy lifting and repetitive tasks. This allows our team members to spend more time performing inspections and quality checks.
According to Kirk Kallio, human resources manager, technology has had huge implications on the dynamic of our workforce.
“Technology has helped us retain employees in an environment that proves to be challenging to remain in. However, with technology, the job has become physically easier, the quality of the product is the same every time, and it allows a diverse workforce to continue working in these jobs that are becoming increasingly less taxing.”
Whether to improve casting quality, energy efficiency or work conditions, Waupaca Foundry uses technology to continuously improve operations, and we will continue to seek out new opportunities and advancements.

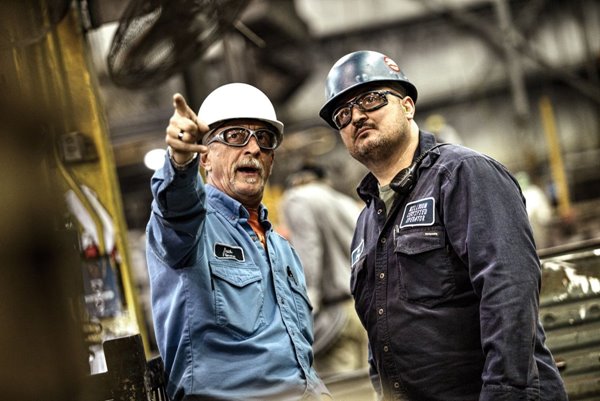