Project Engineer Dave Bean Leads Waupaca Foundry Through a Successful Cupola Replacement
Lydia Engelbreth | Waupaca Foundry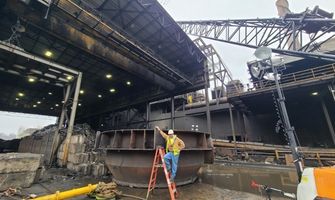_3.jpg)
Dave Bean during the removal phase of the replacement with his "catch of the day" from his 295-foot fishing pole (also known as a crane).
Dave spent a large majority of the past two years working on the replacement of the ductile iron cupola. In any foundry, the cupola is the heart of a foundry, and without it, nothing else functions. Just like a heart pumps blood to all of the major vessels and arteries, the cupola pumps molten iron.
Similar to a heart transplant, the cupola replacement was just as critical. The project was highly anticipated. Both customers and employees were highly impacted. In fact, the replacement carried the highest risk for Waupaca Foundry in 2021. There were many moving pieces that not only required exact precision but coordination between multiple groups. With multiple moving parts that on average weigh 40,000 pounds and more, each must fit within a fraction of an inch. There was no room for error.
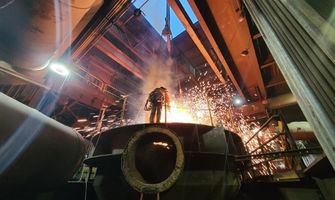
Josey Dorn from Azco cutting free the old cupola during demolition.
This project required removing more than 300,000 pounds of spent material through the roof. New equipment was moved in under a month. Not only did teams work around the clock daily, but they also finished the project ahead of schedule. When asked what this project meant for Waupaca Foundry customers and employees Dave said, “eventually we wouldn’t even be able to use [the cupola], it was in desperate need of replacement. After many years of being in service, there were multiple failure points.” Without replacement, the gray and ductile iron foundry would eventually be unable to operate the cupola. Casting capacity would plummet, affecting Waupaca Foundry being unable to meet customer demand.
Engineering is interwoven with the day-to-day operations at Waupaca Foundry. Dave asserts, “Everything is so complex. Most of the time, people don't know how it all works together.” When asked what his next big project will be Bean said, “My focus is on the other cupola. I have to ask myself, ‘what can we do to keep that piece of equipment operational and keep the gray iron side viable?’” With each project completed, Waupaca Foundry is that much more sustainable and ready to adapt to the evolving customer demand.
Waupaca Foundry is proud to employ more than 120 engineers across nine machining and foundry operations, who are steadfast in and committed to the pursuit of continuous improvement and sustainability.

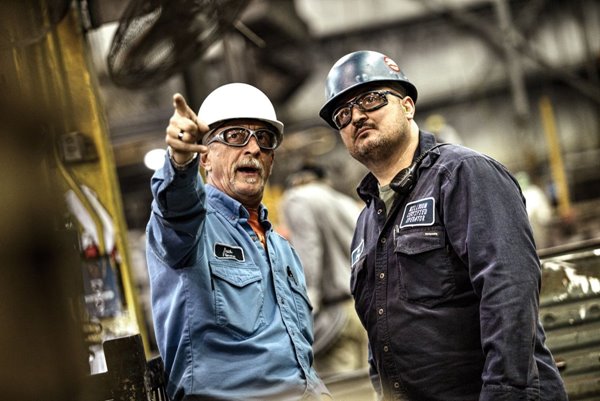
We use cookies and other tracking technologies to personalize content and analyze our site traffic. More information about this is in our Privacy Policy. You can control third party cookies by adjusting your browser settings.