Gray Iron: The Ideal Material for Automotive & Commercial Truck Brakes
Andrew Halonen | Mayflower ConsultingGray cast iron has long stood as the cornerstone of brake systems in automotive and commercial truck applications. Its multifaceted properties make it the go-to material capable of meeting the arduous demands of braking operations. Gray iron is unrivaled in its application for brake components by examining its historical significance, performance metrics, safety features, reliability, economic benefits, and the robustness of its global supply chain.
The Needs of a Brake Material
Brake systems are subject to extreme conditions including high temperatures, friction, and mechanical stress, necessitating a material with specific attributes:
-
High Strength and Durability: To endure the torque loads generated during braking.
-
Stable Mechanical and Frictional Properties: Maintain effectiveness across a broad range of temperatures.
-
High Wear Resistance: Survive the abrasive conditions typical of braking.
-
High Heat Absorption and Thermal Conductivity: Efficiently dissipating the heat to prevent overheating.
-
Vibration Damping: Minimize noise, vibration, and harshness (NVH) for a smoother ride.
-
Minimal Thermal Expansion: Ensure reliable performance consistency.
-
Excellent Machinability: Facilitate cost-effective manufacturing.
Gray iron meets all these critical requirements, making it the ideal choice for brake systems.
History of Gray Cast Iron in Brakes
The use of gray iron in braking systems dates to the early 20th century when the automotive industry was in its infancy. Its adoption was driven by its availability, excellent castability, and cost-effectiveness. Over the decades, advancements in metallurgy and casting techniques have further refined its properties, optimizing gray cast iron for modern brake applications and solidifying its position as a staple material in the industry.
Performance, Safety and Reliability
One can argue that the tire is the most critical safety item on a car because if grip is lost, the vehicle is out of control. Second is the brake system, which is a friction couple consisting of the disc (or drum) and the pad (or liner). Brake engineers are risk averse; reliable solutions are favored over alternatives for most applications.
Gray cast iron has long been relied upon as the primary material solution for discs and drums. Gray cast iron's performance in braking applications remains unmatched. Its high thermal conductivity allows effective heat dissipation, preventing brake fade even under strenuous conditions. Its thermal capacity is critical for long braking events, such as a truck driving down a mountain. The inherent vibration-damping properties reduce the judder for optimal driving performance and noise, offering a quieter and more comfortable driving experience. Additionally, its robust wear resistance ensures long-lasting braking components, which is vital for vehicle safety and reliability.
Composition
The microstructure of gray cast iron, characterized by graphite flakes, offers excellent thermal and mechanical stability. This ensures that brake components made from gray cast iron can withstand the rigors of daily use and extreme braking conditions without significant degradation. Its resistance to thermal cracking further enhances its reliability, making it an invaluable material for consistent and safe braking performance.
Economics
From an economic standpoint, gray cast iron is particularly compelling. 85% or more of the raw material used in gray iron is recycled material, delivering economics and sustainability. Of the thousands of components on a vehicle, few are as readily recyclable to return to its original form and perform without compromise. The efficient production processes and cost-effective raw materials contribute to lower manufacturing costs. The established global supply chain produces competitive product making gray cast iron an attractive option for both manufacturers and consumers.
Global Supply Chain
When vehicle OEMs and Tier suppliers specify components and technologies for the vehicle, a key consideration is the availability of supply. Many vehicles are launched in several countries simultaneously, and common materials reduce variability.
The global supply chain for gray iron is robust and well-established. Foundries worldwide produce high-quality gray cast iron, ensuring a consistent supply of raw materials for brake manufacturing. This extensive network facilitates the swift exchange of technological advancements and best practices, further enhancing the quality and performance of gray iron braking components.
Similarly, the friction materials that work well with gray iron are also available on all continents. Vehicle OEMs reduce their risk when sourcing materials with a robust global supply chain.
Waupaca Foundry: A Leader in Gray Cast Iron Brake Discs and Drums
Waupaca Foundry stands out as the world's largest producer of cast gray iron discs and drums. Here are several reasons behind its leading position:
-
Advanced Technology: Waupaca Foundry harnesses cutting-edge casting and machining technologies to produce superior brake components. Custom-built vertical green sand molding machines are particularly noteworthy for delivering high-quality castings with exceptional consistency.
-
Quality Control: The foundry has stringent quality control measures in place, ensuring that every disc and drum meets rigorous safety and performance standards. Commitment to ISO 9001:2015 and IATF 16949:2016 certifications attest to our dedication to quality.
-
Research and Development: Continuous investment in R&D has enabled Waupaca Foundry to push the boundaries of innovation, creating high-strength materials that facilitate lightweight casting designs, thereby improving both performance and fuel efficiency.
-
Sustainability: Waupaca Foundry prioritizes sustainable manufacturing practices. Responsible procurement and environmental stewardship efforts reduce our overall environmental impact while maintaining high production standards.
-
Customer Focus: With a strong focus on customer needs and satisfaction, Waupaca Foundry delivers tailor-made solutions that meet the specific requirements of automotive and commercial truck manufacturers.
Gray iron remains the ideal material for automotive and commercial truck braking due to its exceptional array of properties, including performance, reliability, and cost-effectiveness. Its unique characteristics make it well-suited to the demanding requirements of brake systems, while the well-established global supply chain enhances its accessibility. Waupaca Foundry's leadership in casting gray iron brake discs and drums exemplifies its commitment to quality, innovation, and customer satisfaction. As the automotive industry continues to evolve, the gray iron material solution will undoubtedly remain a cornerstone of brake system technology, with Waupaca Foundry setting new standards of excellence.
REFERENCES:

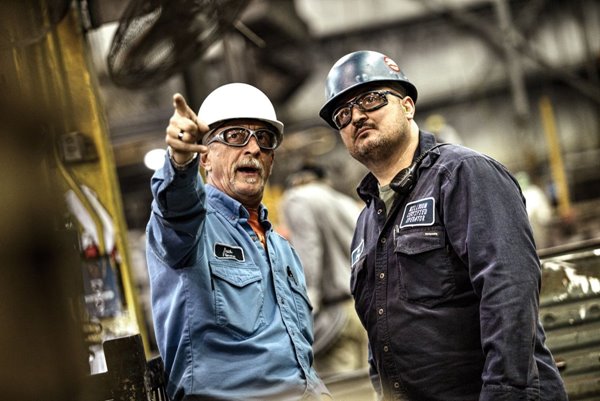