Trends in Lightweighting with Metal Castings
Andrew Halonen | Casting Source May/June 2020
Trends in Lightweighting with Metal Castings
The best applications in lightweighting cut costs while improving performance. Waupaca Foundry achieved success on an automotive steering knuckle, converting an aluminum forging to an optimized ductile iron design that is 20% stronger, 25% stiffer and 40% lower cost, while narrowing the weight delta to an acceptable 1.32-kg increase over the forging.
Despite the resistance, metalcasters are a hardy crowd and still find successes in lightweighting. Communicating success is much easier to me in pictures than words, as was intended at the Metalcasting Congress 2020. In preparation for the presentation, I reached out to my global network and received success stories from the U.S., Bulgaria, Sweden, France, and Canada. Metalcasting lightweighting examples were categorized as material conversions, sheet metal-to-castings, multi-metal, generative design, powertrain influence, and process optimization. Last, we found two new alloy developments that will enable lightweight castings. The best applications in lightweighting cut costs while improving performance. Waupaca Foundry (Waupaca, Wisconsin) achieved success on an automotive steering knuckle, converting an aluminum forging to an optimized ductile iron design that is 20% stronger, 25% stiffer and 40% lower cost, while narrowing the weight delta to an acceptable 1.32-kg increase over the forging. Again, cost is king in most applications, and this example shows that delivering a lower weight than the incumbent is not mandatory to win the sale.
Again, cost is king in most applications, and this example shows that delivering a lower weight than the incumbent is not mandatory to win the sale.
To read more about Waupaca Foundry, click here

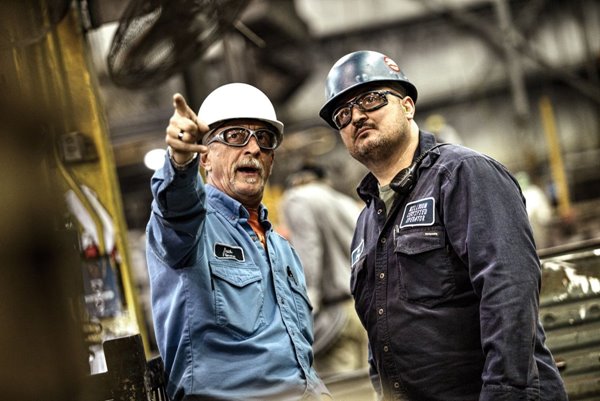