"There are certain castings that are more challenging to cast vertically than they would need to be in rising and gating; as soon as you part a casting horizontally, you can riser and gate in ways not possible with vertical. Some are cost-prohibitive to produce vertically, and some are just better horizontally – it is all about a difference in the way the casting is actually produced.”
Waupaca Foundry Reprises Horizontal Molding For a Great Fit
Janelle Bailey | Waupaca FoundryIt has been over 30 years since Waupaca Foundry has had horizontal molding capabilities. In May of 1967, Waupaca Foundry installed its first vertical molding machine, and by the early 1990s, the last of the horizontal molding machines were removed. Since then the iron casting supplier has become known for high-volume, high quality iron casting production with its in-house design, built, installed, and maintained vertical molding machines.. “As we build new equipment we are constantly looking to add innovative features that add safety, quality, productivity, and reliability,” Vice President of Engineering, Jarrod Osborn.
Horizontal green sand molding is best for large, complex, and lower volume iron castings. Todd Pagel, vice president of operations, explains:
“Lots of time and energy went into investigating the different types of horizontal molding machines available—tight flask, flaskless, etc.—and lots of research went into all of the available options and variables and what would fit best at Waupaca Foundry” offered Curt Literski, Senior Project Engineer at Plant 1, and that keenly sought “fit” was quite literal as well.
Debbie Eckmeter, Vice President of Manufacturing at Sinto America shared: “Sinto was pleased to partner with Waupaca on this FCMX and Handling System, our first in North America. It has been exciting to see this project come together and we are all looking forward to following the results of the horizontal molding machines in Waupaca’s plants. Our team is excited for Waupaca to see improvements in their productivity and continue to strive to see better their bottom line as a foundry.”
While Waupaca Foundry is replacing a 22 x 34 vertical molding machine at Plant 1 with the new horizontal molding machine in that space, the two machines and their space needs are not identical. A number of different layouts were considered to squeeze in enough mold handling conveyance for how long the molds require cooling on the line, which is different for this horizontal processing and pace from the vertical molding process. Overall, the new footprint and total real estate required is slightly greater than the old, but it is due to the handling line, not the actual machine. Much work and preparation was done to fit the entire line wisely and well into virtually the same space with minimal disruption to anything else.
Another consideration is that horizontal molding requires an extraordinary capacity for iron availability and sand delivery to keep up with the 200 molds/hour. This is one of the reasons that it is the first Sinto machine model purchased and installed in the United States. Waupaca Foundry has the capabilities to keep up with iron quantity and sand delivery, prompting consideration of this particular machine, which has the right production requirements and is the best fit for incorporation into the existing facility.
An added, valuable feature is that it can change pattern in cycle, an advantage over the current machines, which create downtime to change the pattern; therein, no productivity is lost while doing a tooling change.
“From the inception of the project, the Sinto America and Waupaca teams have been working closely on planning, designing and executing this project to seamlessly integrate it into Waupaca’s plant,” said Michael Halsband, CEO, Sinto America. He added: “With Waupaca’s experienced manufacturing staff and Sinto’s Smart Foundry technology, we are confident that this system will set new performance standards for speed on horizontal mold machines in North America. We are looking forward to working alongside Waupaca in the weeks to come to make this project a success for both companies.”
“So this capital investment project returns a horizontal molding capacity to Waupaca Foundry but with 35-40 years’ more modern equipment than we previously used,” according to Todd Pagel. This is highly capable, highly productive matchplate molding that could also fit into the existing plant without needing a lot of additional support equipment for gray iron casting production.
Waupaca Foundry operates four foundries in the United States totaling 1,400,000 tons of capacity across 29 vertical and one horizontal molding machines.
#iron-casting
#waupaca
Horizontal green sand molding is best for large, complex, and lower volume iron castings. Todd Pagel, vice president of operations, explains:
Debbie Eckmeter, Vice President of Manufacturing at Sinto America shared: “Sinto was pleased to partner with Waupaca on this FCMX and Handling System, our first in North America. It has been exciting to see this project come together and we are all looking forward to following the results of the horizontal molding machines in Waupaca’s plants. Our team is excited for Waupaca to see improvements in their productivity and continue to strive to see better their bottom line as a foundry.”
While Waupaca Foundry is replacing a 22 x 34 vertical molding machine at Plant 1 with the new horizontal molding machine in that space, the two machines and their space needs are not identical. A number of different layouts were considered to squeeze in enough mold handling conveyance for how long the molds require cooling on the line, which is different for this horizontal processing and pace from the vertical molding process. Overall, the new footprint and total real estate required is slightly greater than the old, but it is due to the handling line, not the actual machine. Much work and preparation was done to fit the entire line wisely and well into virtually the same space with minimal disruption to anything else.
Another consideration is that horizontal molding requires an extraordinary capacity for iron availability and sand delivery to keep up with the 200 molds/hour. This is one of the reasons that it is the first Sinto machine model purchased and installed in the United States. Waupaca Foundry has the capabilities to keep up with iron quantity and sand delivery, prompting consideration of this particular machine, which has the right production requirements and is the best fit for incorporation into the existing facility.
An added, valuable feature is that it can change pattern in cycle, an advantage over the current machines, which create downtime to change the pattern; therein, no productivity is lost while doing a tooling change.
“From the inception of the project, the Sinto America and Waupaca teams have been working closely on planning, designing and executing this project to seamlessly integrate it into Waupaca’s plant,” said Michael Halsband, CEO, Sinto America. He added: “With Waupaca’s experienced manufacturing staff and Sinto’s Smart Foundry technology, we are confident that this system will set new performance standards for speed on horizontal mold machines in North America. We are looking forward to working alongside Waupaca in the weeks to come to make this project a success for both companies.”
“So this capital investment project returns a horizontal molding capacity to Waupaca Foundry but with 35-40 years’ more modern equipment than we previously used,” according to Todd Pagel. This is highly capable, highly productive matchplate molding that could also fit into the existing plant without needing a lot of additional support equipment for gray iron casting production.
Waupaca Foundry operates four foundries in the United States totaling 1,400,000 tons of capacity across 29 vertical and one horizontal molding machines.

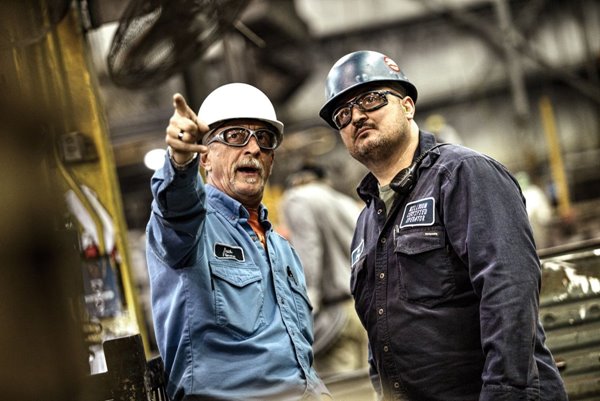
Have a lightweighting, casting conversion, reshoring or other initiative to discuss?
Contact Us
We use cookies and other tracking technologies to personalize content and analyze our site traffic. More information about this is in our Privacy Policy. You can control third party cookies by adjusting your browser settings.