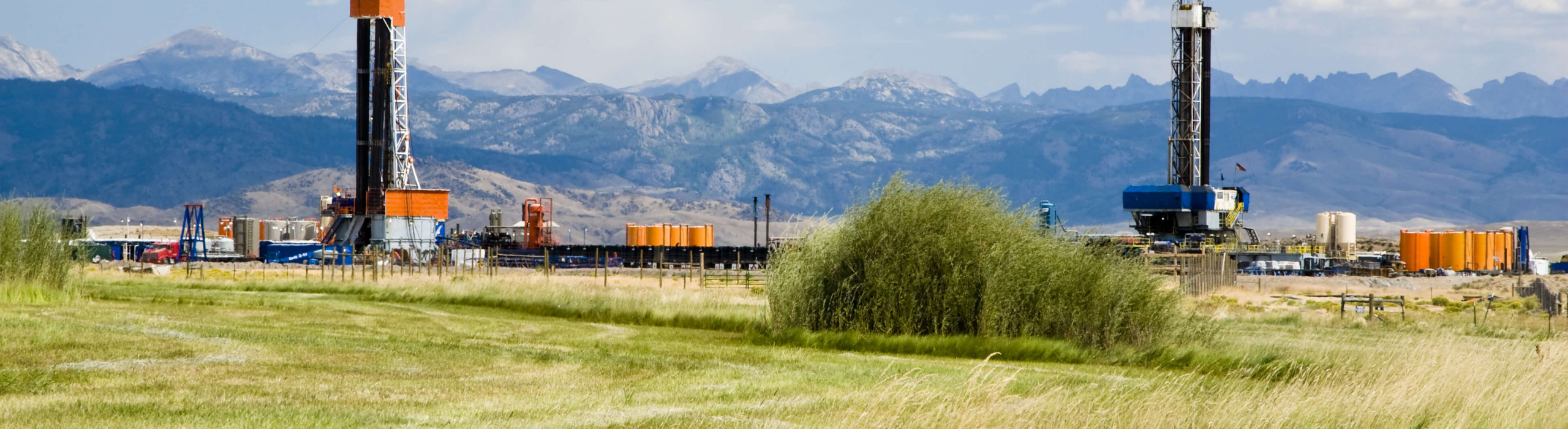
Case Study
Industry Collaboration Leads to Groundbreaking New Product Development
Oil Tool Solutions (OTS) originally sought out a domestic supplier to develop and produce its Hulk clamp used in down-hole oil production. Once in discussion with Waupaca Foundry, OTS changed course in order to expand in new markets by redesigning and creating a smaller-diameter and longer, second-generation clamp.
OTS designs, manufactures, and distributes specialty production tools for the oil and gas industry. One such product is a ductile iron clamp that secures the three-phase electrical cable and capillary tube at the intersections of 31-foot-long sections of pipe, called tubing, that run into land-based wellbores and support the production process of extracting hydrocarbons.
The original HULK product functioned as a standard clamp for a 7" diameter well casing. OTS had success with its initial product offering and was ready to grow with a next generation clamp to expand in new markets. Rather than spending capital to re-tool and onshore the original part to the US, it invested heavily to launch a new product.
OTS soon developed a more versatile clamp that would work in tighter wellbore conditions and combine with a greater combination of cables and capillary tubes. OTS engaged Waupaca Foundry to help finalize a design and produce this smaller-diameter and longer clamp, Hulk SlimCast, while also localizing its supply chain in the US.
Original Clamp Design
The first challenge was to make the clamp not only smaller in diameter to fit 5 1/2" casing applications, but also longer to protect high-value cable. For months, OTS and Waupaca Foundry tested and improved upon a prototype. Simulation software was used to determine production feasibility. Sample iron castings were produced to test just how thin the walls of the clamp could be without compromising its strength and performance. Waupaca Foundry carefully evaluated the wall thickness reductions to assure a quality part could still be produced in production. This exercise continued until it was as thin as possible while retaining the necessary strength to stand up to the harsh downhole conditions.
The second challenge was to prove that the casting could be produced without a core. The first generation Hulk clamp, like the next generation Hulk SlimCast, required holes for hinge pins as well as for latching swinging bolts that operators utilize to assemble and secure the clamp around the pipe and cable on location. The first generation Hulk clamp used a core in addition to machining to drill and tap the holes. This was not value added and presented waste in the value stream. To eliminate the need for a core, the tooling engineering team added draft in several locations and relied exclusively on machining after the part was cast to drill and tap the pin holes. This eliminated one cost driver and offered immediate piece price savings.
Lastly, the Hulk SlimCast clamp is made using high-strength ductile iron, which is more durable and resistant to impact fractures. The material and casting design solution enables Hulk Slimcast to perform in the most unrelenting conditions.
The result is a brand-new part, called Hulk SlimCast for 5-1/2" wellbores, which is smaller in diameter than its predecessor for 7" well casings, but longer in length and with thinner walls. This innovation is extremely adaptable to multiple ESP cable and capillary specifications, all the while standing up to the rigors of use.
And, as a bonus, the Hulk SlimCast design is capable of several configurations without requiring individual foundry tooling for each configuration. The result is considerable cost savings in tooling dollars.
This project was at high risk for failure—largely unachievable—if it were not for finding a manufacturing solution to pour a ductile iron casting with thin sections, tight-diameter holes, and tight tolerances. The collaboration between two domestic companies, using advanced technologies, ultimately enabled market share entry and growth, as well as:
- Reduced tooling cost by 75%
- Reduced casting weight by 12% compared to initial SlimCast design
- Reduced supply chain risk
- Localized supply chain resulting in increased speed to market by 4 months
- Reduced inventory risk and improved cash flow