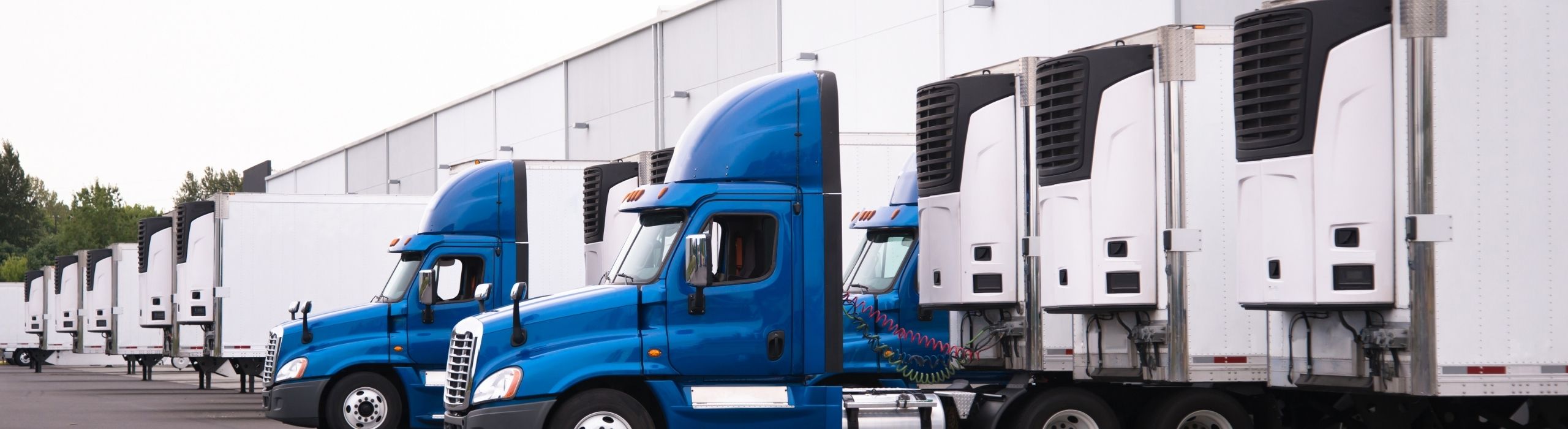
Case Study
Innovation and Problem-Solving Mitigate Supply Chain Risk
Through collaborative engineering and a prototype 3D-printed core assembly, Waupaca Foundry provided a solution that could improve quality, delivery and cost for a compressor body already in production. It also meant reliably changing the iron casting manufacturing process from horizontal to vertical molding, as well as reshoring the part to a U.S. supply base—with complete peace of mind.
A global technology and engineering manufacturer that provides commercial refrigeration innovations for large grocers and supermarkets was faced with disruptions in its supply chain. It offers complex compressor products that help protect food quality and safety, while improving energy efficiency. The compressor body weighs 202 pounds (92 kg) and requires helium leak testing, post-machining. Despite dual sourcing its compressor bodies both in the U.S. and Europe, the manufacturer continued to experience quality issues and downtime.
Waupaca confronted the challenge by using simulation software to explore various solutions for improving the manufacturability of the complex gray iron casting. Through persistent problem-solving supported by iron and sand flow simulation software, Waupaca pursued a unique core package design. Foundry engineers generated a 3D-printed core prototype, instilling customer confidence that the redesigned core package was a reliable solution for improved casting quality on a vertically parted molding machine.
Through an innovative core package design and process change to a vertically parted iron casting solution, the commercial refrigeration manufacturer confidently invested capital to change suppliers. In doing so, the instability in the manufacturer’s supply chain was addressed by reshoring a compressor body, that was already in production, with a more stable, long-term partner, resulting in better quality at a lower cost. Ensuring on-time castings and eliminating recurring downtime has generated valuable peace of mind.
- Reduced internal scrap.
- Consistent wall thickness offers safe compressor operation.
- Consistent dimensional control and surface finish improves machine tool life.