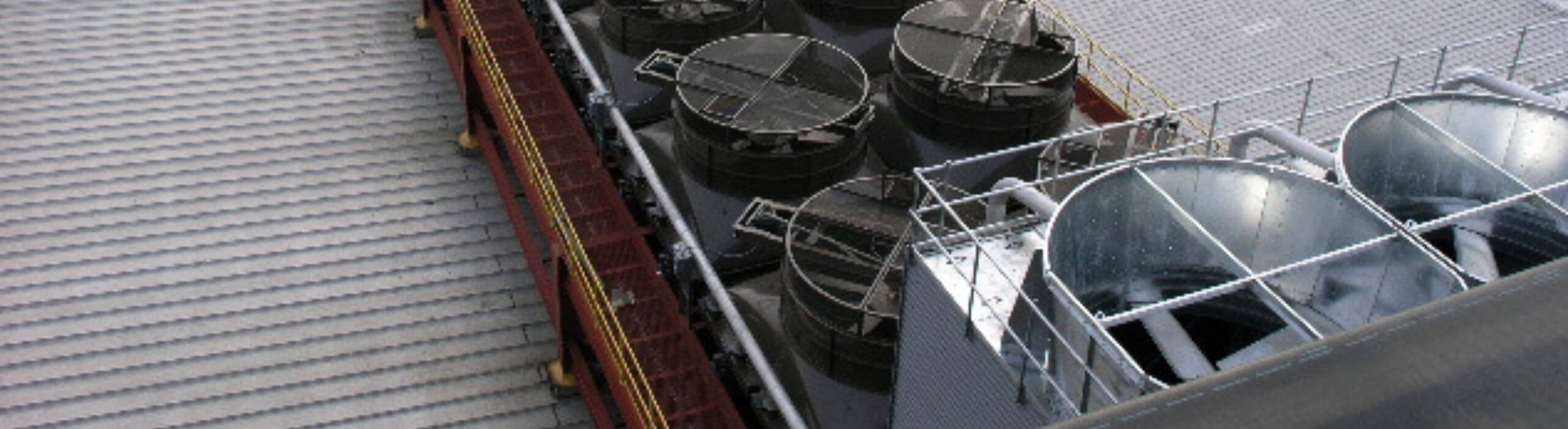
Waupaca Foundry Sustainability Commitment
Achieved Energy Reduction Target
Warm Reception For Heat Recovery Project
Every year the Waupaca Foundry plants across the U.S. melt more than 2.2 million tons of scrap metal. As you can imagine, this intensive energy process gives off an abundance of heat. Thanks to a heat recovery loop added to the cupola melting system at Plant 1, heat doesn’t go to waste.
Since December 2008, Plant 1 located in Waupaca, Wisconsin, has used the heat from its cupola iron-melting process to provide approximately 70 percent of the plant’s space heating requirements for a typical winter, as well as heat for 100 percent of the plant’s hot water needs.
Historically, foundries dispelled “waste heat” into the atmosphere to lower melt system temperatures prior to air pollution control equipment. Today, Plant 1 uses its waste heat to increase the temperature of a water/glycol solution flowing through an installed network of coils within the facility air makeup units.
The project benefits are economical and environmental, offering annual heating savings and an annual reduction of 4,600 metric tons of carbon dioxide. After two years, the project has paid for itself and earned Waupaca Foundry the 2009 Wisconsin Governor’s Award for Excellence in Environmental Performance.
In December of 2008, Waupaca Foundry Plant 1 added a closed-loop heat recovery system that, within two years, has already paid for itself in energy savings.
- Provides nearly all the building heat for winter months and year-round hot water.
- Helps to offset annual heating costs.
- Annual reduction of 4,600 metric tons of carbon dioxide.
- Received the 2009 Wisconsin Governor’s Award for Excellence in Environmental Performance.