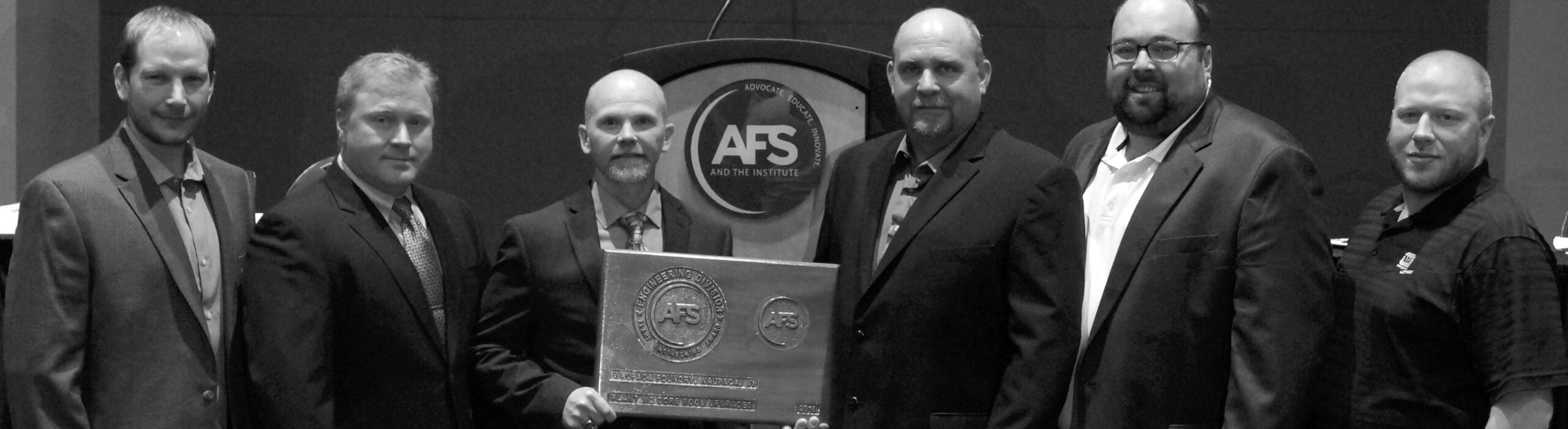
Waupaca Foundry Earns Industry Awards
Component Supplier Honored For Metalcasting Excellence
(WAUPACA, WI) APRIL. 25, 2017 — Waupaca Foundry, has been honored with two distinctions by the American Foundry Society's (AFS). At the 121st Metalcasting Congress, it will receive the Divisional Plant Engineering Award for core room expansion improvements at two gray iron foundries located in Waupaca, Wisconsin. Additionally, the iron casting supplier earned Best In Class for a ductile iron suspension casting converted from aluminum that achieved one of the Detroit Big Three's lightweighting objectives for a major automotive platform. These awards are representative of Waupaca Foundry's commitment to manufacturing innovation and a longstanding culture of continuous improvement.
Waupaca Foundry earns Plant Engineering Award
This award recognizes a company's achievements in planning, installation, operation and maintenance of metalcasting equipment and processes. It also encourages the advancement of technical expertise in operating and maintaining metalcasting equipment.
From 2014 to 2016, the iron casting supplier expanded core production at its Waupaca-based gray iron foundries which increased quality, production efficiency, and worker safety and comfort. Improvements also allow the foundry to expand to meet future customer demand. Upgrades were made at plants located at 406 N. Division St. and 1955 Brunner Drive in Waupaca.
All manufacturing workflows and equipment were designed, built and installed by Waupaca Foundry engineers allowing maximum production flexibility and the ability to customize processes for customers. "Among our highest priorities is to create an environment where our team members contribute ideas to achieve benchmark business results," said Rick Sutton, vice president of operations.
Waupaca Foundry earns Best in Class Casting award
A lower control arm assembly casting produced for a Detroit Automotive OEM, earned Waupaca Foundry AFS' annual casting competition Best In Class award. The suspension component was converted from aluminum to a high-strength ductile iron casting to achieve lightweighting objectives. By using Hitachi Metals' HNM™ high-strength iron material solutions and design support, Waupaca Foundry reduced component weight by 25%, reduced cost, and relieved a supply chain disruption to the OEM.
Scaling production to meet demand is a highly collaborative process between the OEM and its supplier base. "We were able to create a sustainable casting solution for a high volume machined component," said John Weisbrock, executive vice president of sales, marketing and supply chain management. "Our advanced alloys and design support offers customers a cast iron solution over aluminum that not just meets, but exceeds weight reduction targets and performance requirements," Wiesbrock said.
"Our customers seek collaborative casting design and innovative materials solutions that add value to their products," said CEO Mike Nikolai. "These industry awards confirm that our teams are delivering consistent, top tier quality and service that leads the industry."
The American Foundry Society also recognized Waupaca Foundry Retired President and CEO Gary Gigante with the Peter L. Simpson Gold Medal for long-term contributions to the sustainability of the metalcasting industry through environmental stewardship, technological advances, and the development of people in the industry. Additionally, Director of Research and Process Development Gregory Miskinis will receive the Award of Scientific Merit for major contributions to the metalcasting industry through industrial research, mentoring newcomers to the industry, and service to the Northeastern Wisconsin chapter of AFS.
Waupaca Foundry casting solutions at the 121st Metalcasting Congress
In addition to these awards, Waupaca Foundry is featuring innovative castings at the 121st Metalcasting Congress. These iron castings demonstrate Waupaca Foundry's range of castings on display demonstrate Waupaca Foundry's range of capabilities to solve lightweighting objectives, convert weldments and forgings to iron castings, and reshoring initiatives. Castings on display include examples of:
Lightweighting:
- A ductile iron differential carrier for a light truck application achieved 11% weight reduction;
- A gray iron transmission case for class 8 commercial trucks dropped mass by 15%;
- A ductile iron lower control arm (converted from aluminum) for a midsize passenger car platform cut weight by 25%.
Conversions:
- A crankshaft for a midsize car engine platform was converted from a forging to a ductile iron casting;
- A 9-piece weldment was converted to a single ductile iron alternator housing assembled in emergency response vehicles and specialty vehicles;
- Used in industrial applications, an electric motor housing, which was once ductile iron, was converted to gray iron.
Castings reshored:
- Production of an air disk brake and crankshaft damper on Class 8 commercial trucks was localized to the United States, thus reducing inventory and total landed manufacturing costs;
- A sprayer hinge used in ag and turf applications was converted from a two-piece assembly to a single ductile iron casting.
For more information on Waupaca Foundry's castings solutions, visit booth #538 at Metalcasting Congress, April 25-27, 2017 in Milwaukee, Wisconsin.
###