Waupaca Foundry casting innovation earns national award
Mary Schmidt | Waupaca FoundryAn advanced manufacturing process, known as 3-D printing, has won national recognition for Waupaca Foundry. The American Foundry Society (AFS) recognized Waupaca Foundry’s Tyler Nooyen for co-authoring a paper on the use of 3-D printed cores to manufacture iron castings. The paper was the first definitive study to compare dimensional capabilities of conventional cores to 3-D sand-printed cores.
The study earned the Ray H. Witt Management Award which recognizes information, knowledge, processes, or technologies that have a positive impact on the metalcasting industry as a whole.

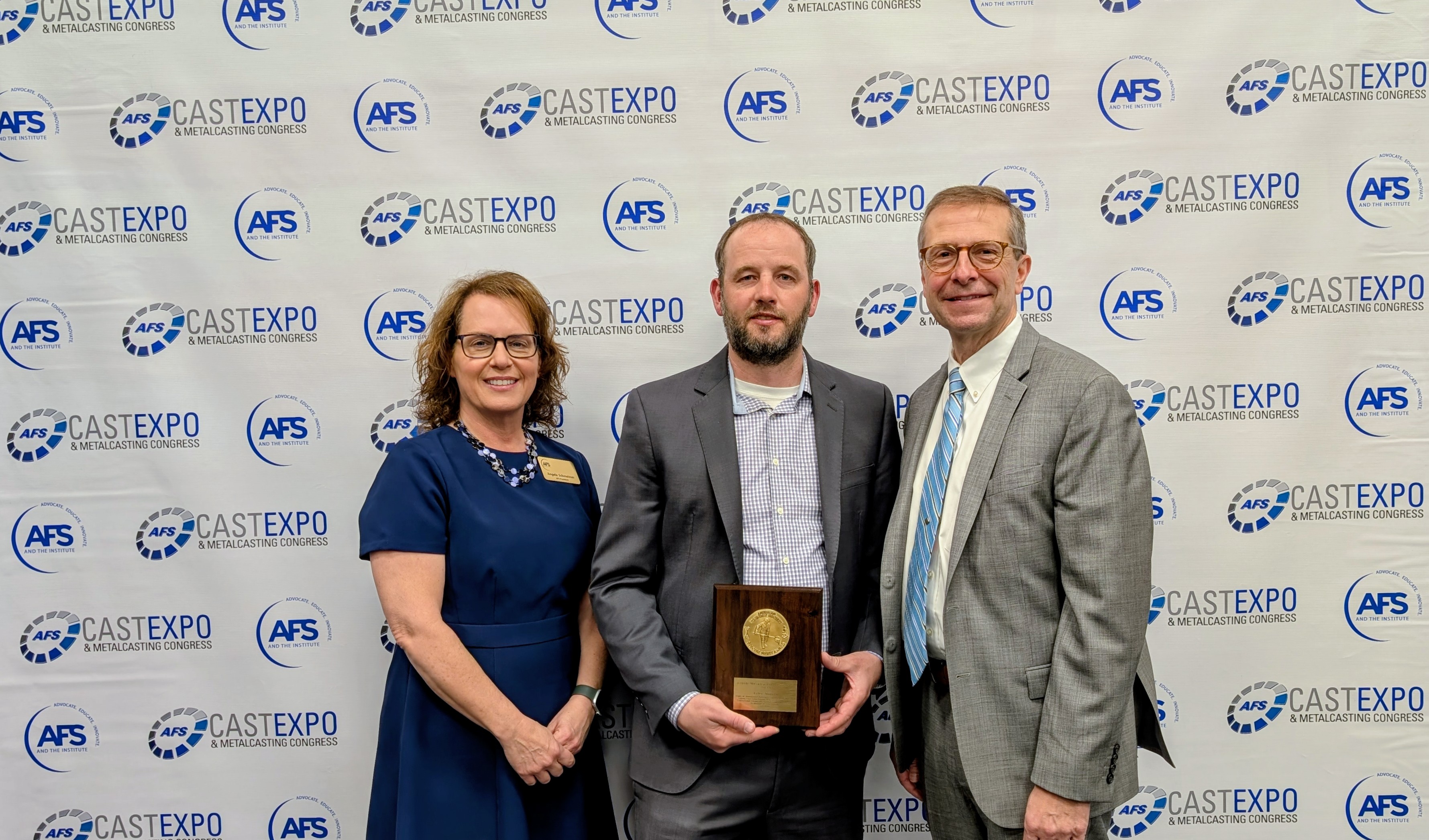.jpg)
Pictured left to right: Angela Schmeisser, Immediate Past President for the AFS Board of Directors, Tyler Nooyen, Plant 1 Assistant Plant Manager, and David Gilson, President for AFS Board of Directors.
In the study, the team outlined a series of test pours that incorporated 3D printed cores produced using multiple methods from different facilities. The cores were all used to produce castings at Waupaca Foundry plants. The team then evaluated multiple-dimensional studies to help quantify the capabilities of the different manufacturing processes.
“The key to the study was to better understand the potential advantages that 3-D printing had to offer,” Nooyen said. “Ultimately, the goal is for design engineers to work together with foundry engineers to fully leverage the advantages of this relatively new process. Hopefully, this data helps facilitate that.” Nooyen has worked at Waupaca Foundry since 2005 and is the assistant plant manager at Plant 1.
In iron casting, a core is used to create internal cavities or intricate features inside the final casting — basically, any hollow section or complicated internal geometry that the mold itself can’t easily form. They are traditionally produced using hard tooling and sometimes require core assembly and finishing before use in the manufacturing process to make iron castings. Using additive manufacturing, or 3-D sand printing, eliminates tooling and associated costs, eliminates manual core assembly steps, and increases quality to meet tighter tolerance specifications from customers.
In green sand molding processes, some cores experience core separation and inadequate adhesion, causing core scrap. Other cores could have excessive flashing, which, after the iron castings were poured and cooled, needed manual grinding in the mill room. Still other cores with thin walls experienced a high rate of damage, which also led to scrap and waste.
Currently, 3-D sand printing is considered a hybrid approach to core production. There is little confirmed documentation outlining the dimensional tolerances and precision using the process until this study identified guidelines for casting design engineers.
“We have used 3-D printing before, but primarily for prototyping,” said Director of Lean Operations David Scott. “Adopting 3-D sand printing isn’t just about new technology — it’s about transforming how we approach manufacturing challenges. It gives us the flexibility to reduce lead times, lower costs, and offer more innovative solutions to our customers. It’s another step toward building the foundry of the future.”
For one customer, the additive manufacturing process provided a solution to supply chain disruption. A global manufacturer that provides refrigeration innovation needed a reliable partner to produce a complex compressor body. Waupaca used simulation software to explore solutions for manufacturing the 202-pound gray iron casting. By using iron and sand flow simulation software, Waupaca produced a unique core design and generated a 3D-printed core prototype. The result was a piece that could be produced on a vertically parted molding machine that maintained consistent wall thickness, consistent dimensional control and surface finish. The manufacturer was able to use the new process to produce a complicated part with a reliable manufacturing partner and reduce costs and increase quality at the same time.

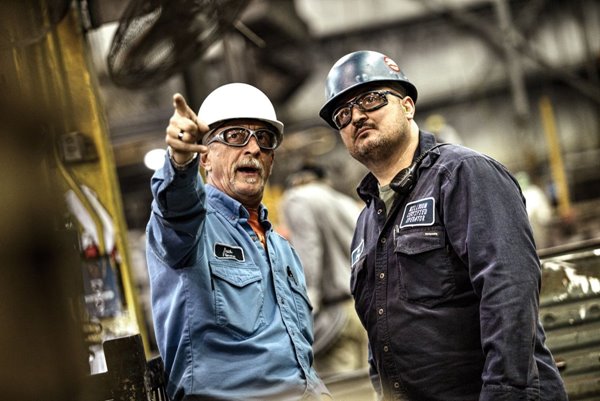